Total Quality Management
Basic Approach of Quality Management
The Takenaka Group conducts its business activities based on "quality management."
Since the founding of our business, the mainstay of Takenaka has been specialization in building construction and an integrated design-build method of delivery. Originating in the toryo (master builder) spirit of shrine and temple carpenters, this spirit is a strong belief that the toryo, "taking responsibility to the end for any work that is undertaken," will possess not only the techniques and knowledge to construct buildings, but also procure a wide variety of materials and have the leadership skills to lead the organization in accomplishing large jobs. This goes hand in hand with “quality management."
For the Takenaka Group, "quality management" means "Earn client satisfaction and society's trust through management that persists in stressing quality and challenging creation of new environments" (Total Quality Management Basic Policy). The "quality" in quality management does not simply refer to the quality of buildings, but also means the "quality of overall corporate activities" as a social entity. Unwavering in our commitment to improving "quality," the Takenaka Group continues to implement "quality management."
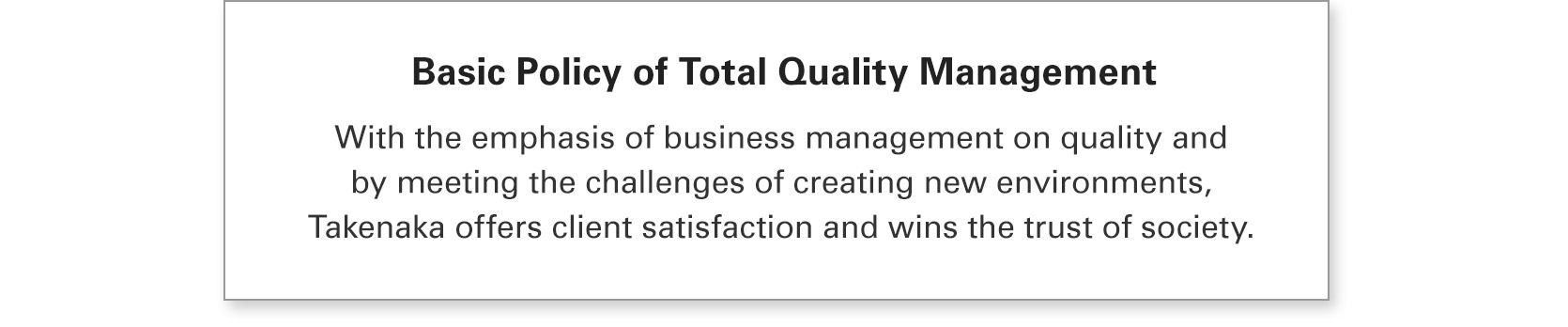
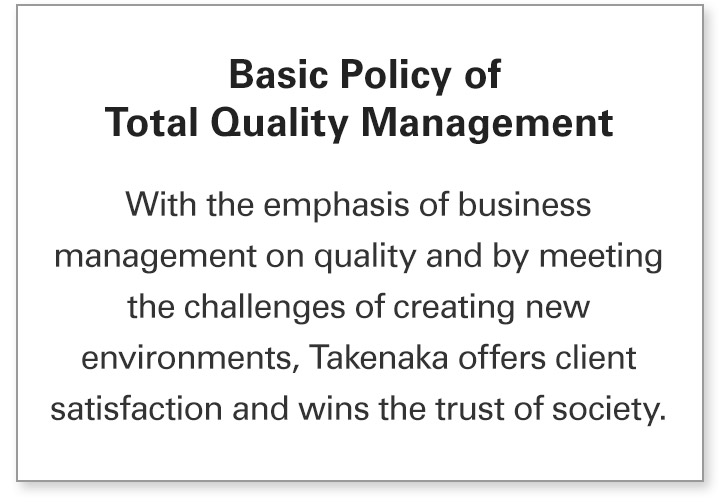
About: Takenaka Quality Management (TQM)
In the mid-1970s, Takenaka introduced and had long been promoting Total Quality Management (TQM) as a scientific management method.
By 2015, there was a need to take TQM to a new level for the long-term development of the Takenaka Group, so activities up until that time were restructured as “TQM in Takenaka's Business Management,” which was based on our Total Quality Management Basic Policy, and Takenaka Quality Management (TQM) was established.
TQM aims to improve the quality of all corporate activity, continuously contributing to society.
It has been divided into four :
- Business Plan Management (Policy Management)
- Customer Satisfaction (CS), Employee Satisfaction (ES), and Corporate Social Responsibility (CSR)
- Quality Assurance and ISO
- Basis of corporate capabilities
Here are the details.
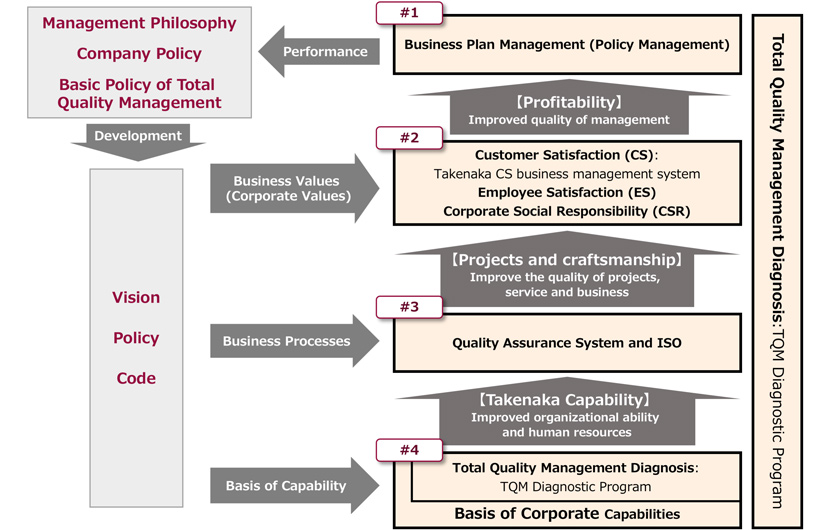
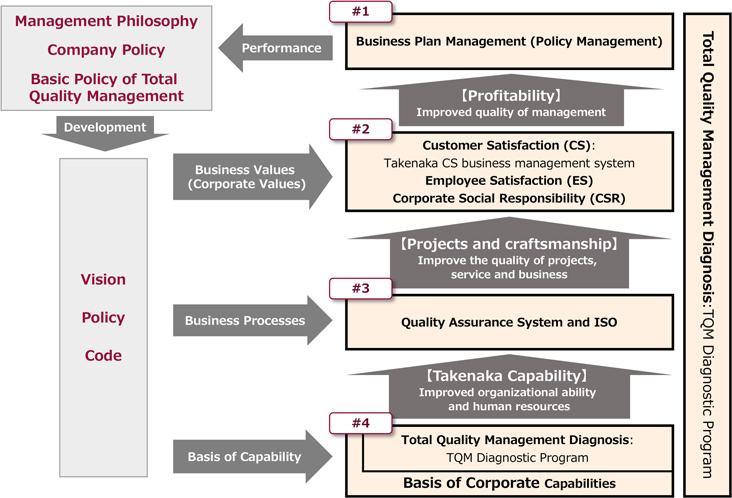
#1
Business Plan Management (Policy Management)
Promotion of the business plan management needed for corporate activities, in addition to daily and cross-functional management, and implementation of the Total Quality Management Diagnosis (TQM Diagnostic Program) by top management.
#2
Customer Satisfaction (CS):the Takenaka CS business management system
Employee Satisfaction (ES)
Corporate Social Responsibility (CSR)
Promotion of customer satisfaction (CS) as well as employee satisfaction (ES) and corporate social responsibility (CSR), for satisfactory long term relationships with all stakeholders including clients.
#3
Quality Assurance System and ISO
Standardization of business execution processes along with the maintenance and operation of a quality assurance system that guarantees all stakeholders including clients, high quality architecture and service.
#4
Total Quality Management for Human Resources Development: TQM Education Program
Basis of Corporate Capabilities
Development of human resources looking ahead to the mid and long term in accordance with systemized TQM educational programs which include QC circles in order to maintain and provide a basis for stronger corporate capabilities and business execution.
History: TQM
1976 | Inauguration of TQC |
---|---|
1977 | Formulation of "Quality Assurance Manual" Start of QC circle activity |
1979 | ![]() Dr. Deming visits Takenaka offices |
1983 | Formulation of Quality Assurance Standardization System Start of Client Satisfaction Survey |
1988 | President Ren-ichi Takenaka (at the time) awarded the “Deming Prize for Individuals” |
1992 | ![]() |
1996 | Name changed from TQC to TQM (Total Quality Management) |
2001 | Start of Customer Satisfaction Survey (revised from the previous Client Satisfaction Survey) |
2009 | Formulation of “Total Quality Management Basic Policy” Revision of Quality Assurance System (combining the ISO quality management systems) |
2015 | Formulation of “TQM; Takenaka Quality Management” |
2016 | Start of participation to “Nationwide QC Circle Conference” sponsored by Union of Japanese Scientist and Engineers. Came 3rd overall in “the 9th JUSE Quality Management Level Research” sponsored by Union of Japanese Scientist and Engineers and NIKKEI Inc. |