Decarbonization
Contents
- Ⅰ. Toward the realization of a decarbonized society
- Ⅱ. CO2 reduction in our own business activities
- Ⅲ. Contributing to customer decarbonization through construction
- Ⅳ. Collaboration in the supply chain
- Ⅴ. Technological development that contributes to decarbonization
- Ⅵ. Renewable energy supply projects
Ⅰ. Toward the realization of a decarbonized society
Takenaka Corporation recognizes that decarbonization and climate change mitigation are among the most important issues in realizing a sustainable society. We will therefore promote energy conservation and the use of renewable energy throughout the value chain to reduce greenhouse gas emissions. At the same time, we will also work on design methods and construction techniques that adapt to climate change.
1. Takenaka Group long-term CO2 reduction targets
We aim to achieve carbon neutrality throughout the Takenaka Group and our entire supply chain by 2050. In December 2019, we established a long-term CO2 reduction target and began our efforts, raising the target value in 2021 and aiming for carbon neutrality in 2050. In December 2022, furthermore, we set new medium- to long-term targets for the entire Takenaka Group (consolidated).
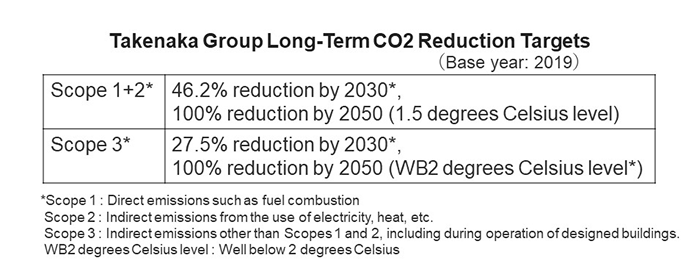
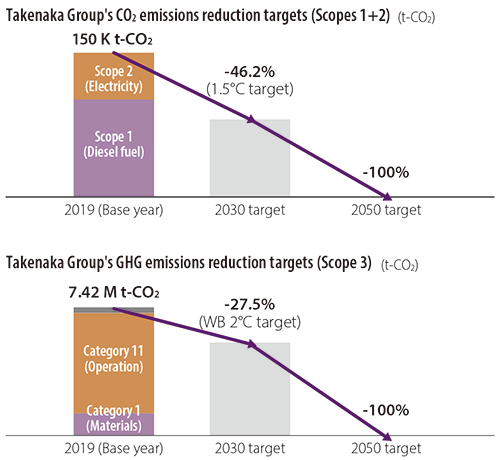
The interim targets we aim to achieve by 2030 are at a level that meets the global common goals of the Paris Agreement.
- ・The total of Scope 1 and Scope 2 due to our own energy use will be reduced by 46.2% compared to 2019 (1.5℃ level)
- ・Total Scope 3 emissions from others will be reduced by 27.5% compared to 2019 (WB 2℃ level)
External assessments
Obtaining SBT certification
In March 2024, Takenaka Group's emission reduction targets (Near-Term Science-Based Targets) were certified by SBTi as being in line with the 1.5℃ greenhouse gas reduction target (Scope 1, 2).
2. Road map towards achieving targets
In order to realize a decarbonized society, we are formulating a road map to achieve carbon neutrality by 2050, and we are considering strategies based on medium- to long-term scenarios while referencing the Japanese government's Green Growth Strategy. Continually reviewing our road map in line with social conditions, we are working to incorporate specific measures and business plans to achieve this target.
Ⅱ. CO2 reduction in our own business activities
We place the highest priority on reducing Scope 1 and Scope 2 CO2 emissions associated with our own energy use as our corporate responsibility.
1. Initiatives in construction work
The largest amount of CO2 emissions from the Takenaka Group's business operations comes from activities at construction sites. In order to accelerate CO2 reduction efforts at these places, we established Challenge! Zero CO2 work sites in 2022, and we began adopting energy-saving construction methods and introducing renewable energy. From February 2023, Takenaka has been accelerating its efforts to use green electricity, in principle, at all new construction sites.
Specific initiatives
- ・Creating construction plans using a “CO2 reduction items list”
- ・Introduced a “CO2 emissions monitoring system” and used it to manage targets for reducing CO2 emissions from construction work.
- ・Challenge! Zero CO2 signs are being posted on temporary fences at construction sites
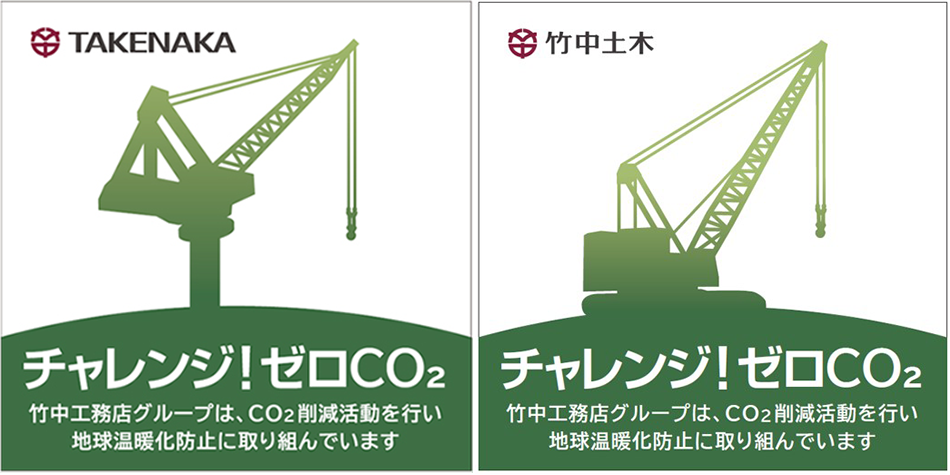
CO2 emissions monitoring at construction sites
The main sources of CO2 emissions at construction sites are diesel fuel used by heavy construction machinery and on-site vehicles, electric equipment such as tower cranes, and electricity used in offices, but the volume of emissions fluctuates greatly depending on the progress of construction and the machinery used. In order to promote activities to reduce CO2 emissions, we began introducing a “CO2 emissions monitoring system” in 2023 that quickly grasps the status of energy use and CO2 emissions at each site. When a person in charge inputs data such as a machine operating status, CO2 emissions are automatically calculated and aggregated, making the situation of the entire company visible.
Furthermore, some construction sites have introduced the IoT device Dondake to save labor and improve accuracy in data entry. This device is attached to a machine's battery, detects the electric current value, and sends a signal to the CO2 emissions monitoring system to automatically ascertain the operating status of the machine. In the future, we will proceed with introducing this to many work sites.
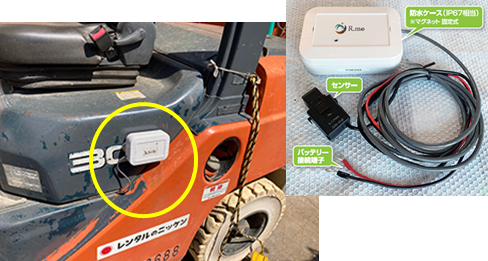
Temporary house Ecofis Resist that saves energy
Ecofis Resist, an energy-saving temporary office for construction sites, was jointly developed with Asahi Kizai, an affiliated company that rents construction materials and equipment, and it is gradually being adopted. Due to improved insulation performance and the introduction of LED lighting, it is expected to reduce CO2 emissions by approximately 20 percent compared to conventional methods, and it is also fire resistant.
In order to further improve insulation performance and save energy, options include insulation panels for joint areas, windows and door screens that allow natural breezes to pass through, and solar panels that prevent roof temperatures from rising while generating electricity.
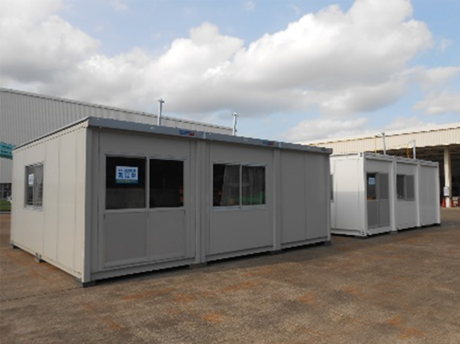
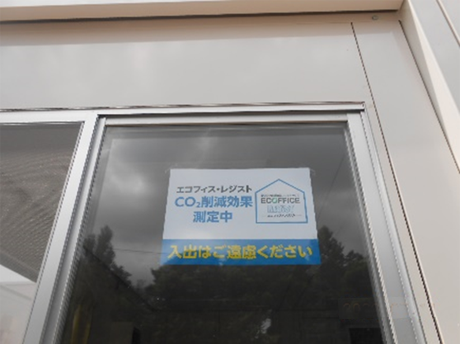
Fuel-efficient operation of heavy construction machinery and construction vehicles
Together with our partner companies, we are working to reduce the amount of diesel fuel used by conducting educational activities such as training on operating heavy construction machinery and construction vehicles to raise the awareness and skills of workers.
Installation of construction vehicle waiting yard
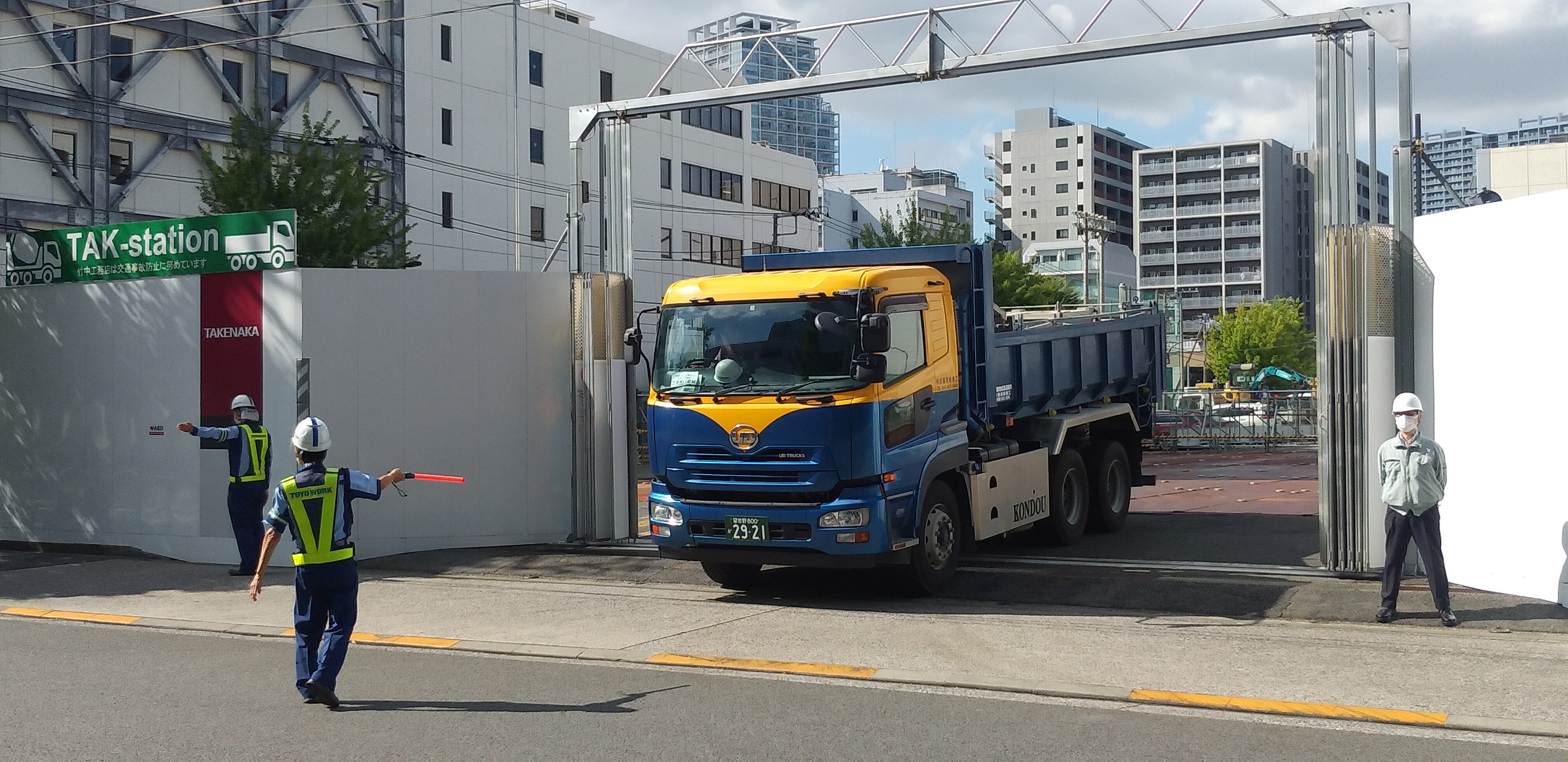
Many large vehicles enter and exit construction sites to deliver materials and other things, but at construction sites in urban areas, vehicles waiting on the road can cause traffic congestion. We are working to lease surrounding land for some construction sites in Tokyo and set up TAK-station waiting yards for construction vehicles. This not only eases traffic congestion, but also reduces CO2 emissions by stopping idling time.
CO2 reduction technology associated with waste emissions
Reducing the amount of construction waste and by-products, such as excavated soil, will also lead to a reduction in CO2 emissions when transporting it off-site by vehicle. The technologies we have developed, TSP-eco and TSP-ZERO, can significantly reduce the amount of sludge generated during underground construction and are expected to have particularly large effects.
We are also working to reduce CO2 emissions associated with waste emissions by installing sensors to detect when waste stocking containers are full, thereby reducing the frequency of collection, and by working with partner companies to shorten collection and transportation routes.
Introduction of renewable energy at construction sites
Scope 2 reduction
By fiscal 2022, approximately 30 percent of the electricity used at our construction sites will be renewable energy, and construction that begins on or after February 1, 2023 will, in principle, use green electricity derived from renewable energy.
Scope 1 reduction
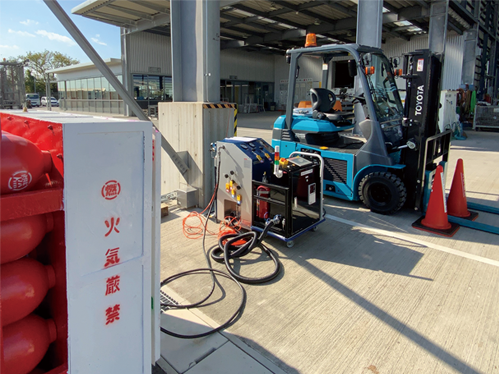
Of the CO2 emissions at construction sites, 75 percent comes from diesel oil used as fuel for construction machinery, dump trucks, and other vehicles. In order to reduce this, efforts are being made to introduce alternative fuels (HVO, etc.), which are being examined with trials being conducted.
Main initiatives
- ・Trial introduction of RD100 fuel (100 percent renewable diesel fuel)
- ・Trial of “fuel cell forklift” using hydrogen as fuel
2. Initiatives at our own offices
We have set targets at our offices to reduce energy consumption from the previous year. Along with continuously implementing energy-saving initiatives, we have also introduced solar power generation at major offices. Reducing CO2 emissions through operational improvements, we are in turn improving the environmental performance of our buildings through renovation and reconstruction, and we have also acquired certifications such as the Building-Housing Energy-efficiency Labeling System (BELS).
- Building-Housing Energy-efficiency Labeling System (BELS): Based on Guidelines for Labeling Energy Consumption Performance of Buildings, a third-party assessment organization evaluates and certifies the energy-saving performance of new and existing buildings.
- ・Net ZEB: Buildings whose energy consumption is 50 percent or less of the standard value and whose energy balance is zero due to renewable energy
- ・Nearly ZEB: Buildings whose energy consumption is less than 50 percent of the standard value and whose net energy consumption is less than 75 percent due to renewable energy
- ・ZEB Ready: Buildings with energy consumption less than 50 percent of the standard value
Takenaka Central Building South (Tokyo)
Completed in 1999, this office building has been completely renovated into a smart building, reducing CO2 emissions by 50 percent. It reopened in October 2022 as a centralized operating base for seven Takenaka Group companies.
In the renovation, we introduced a variety of solution technologies, including Bilcomi® Plus, which we developed, in order to respond to social needs, such as decarbonization and work styles becoming more diverse. In addition to aiming to further reduce CO2 emissions through future operations, the facility will be used as a venue for the development and demonstration of smart-building-related technologies.
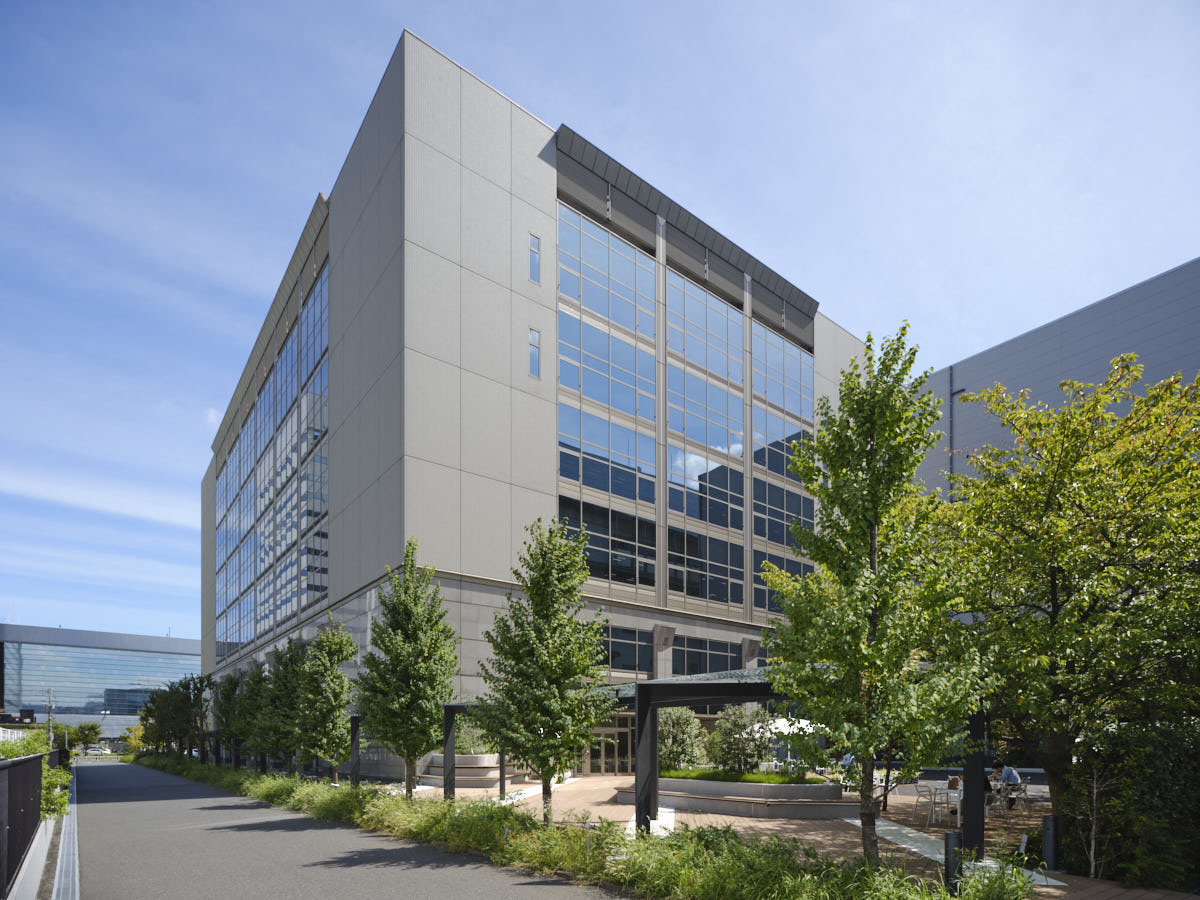
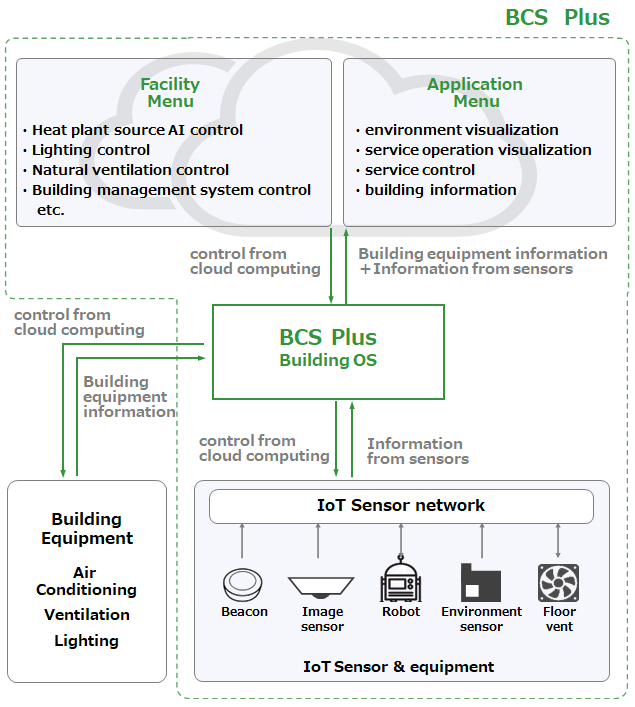
Osaka Head Office Mido Building (Osaka Prefecture)
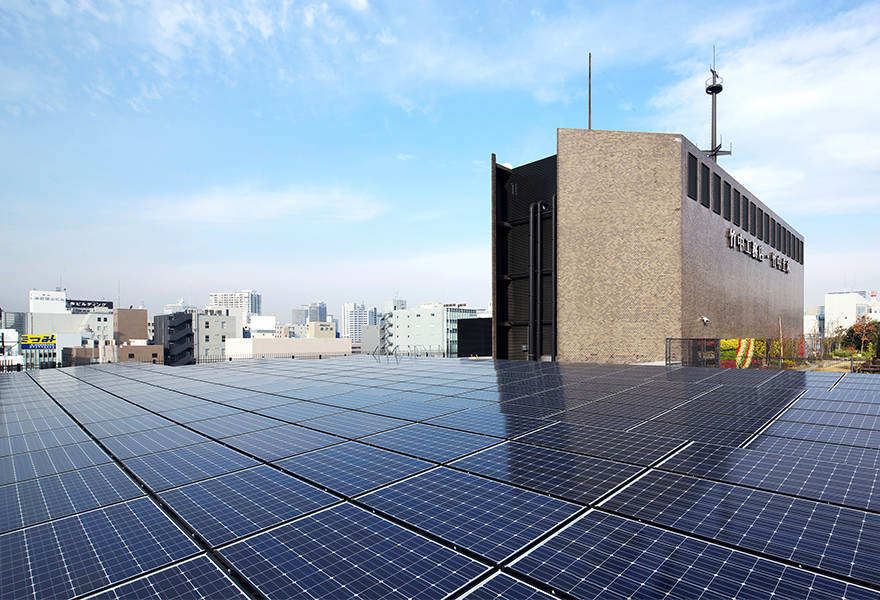
In addition to solar power generation, the Mido Building (completed in 1965), which houses seven Takenaka Group companies, has been using “carbon-neutral city gas” since October 2021. This means the CO2 emitted during the entire process of natural gas extraction, transportation, production, and combustion has been offset with credits. Additionally, a large-scale renovation was carried out between 2014 and 2018, transforming the building, which is over 50 years old, into an attractive workplace.
Higashi-Kanto Branch (Chiba Prefecture, Net ZEB)
At our Higashi-Kanto Branch, which was renovated to become a ZEB system in 2016, we introduced technologies developed in-house, such as radiant heating and cooling systems that directly use geothermal heat and solar heat, and ultracompact desiccant air conditioners, as well as improvements in performance through equipment and exterior updates. By reviewing work styles, we have reduced energy consumption and achieved net-zero energy.
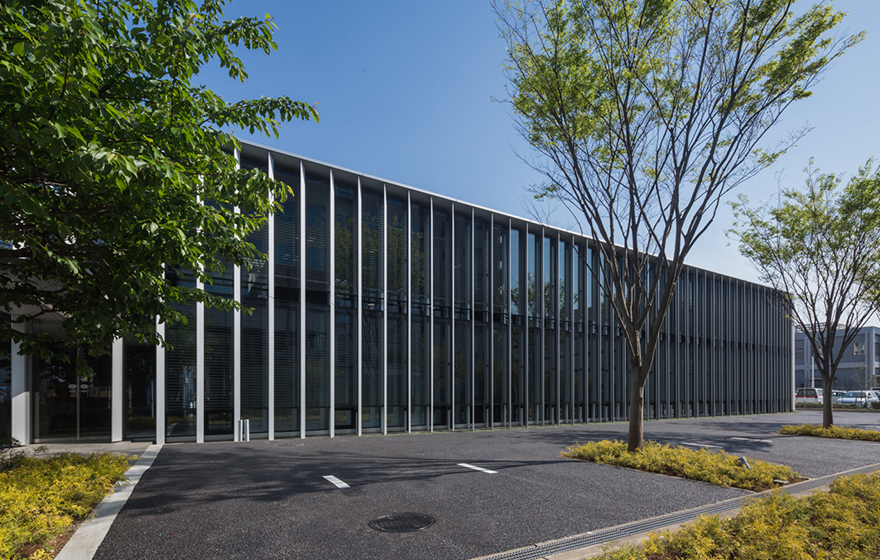
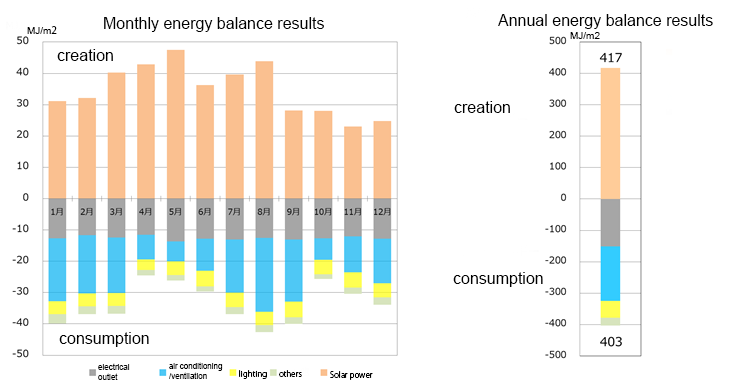
Tokyo Main Office (ZEB Ready)
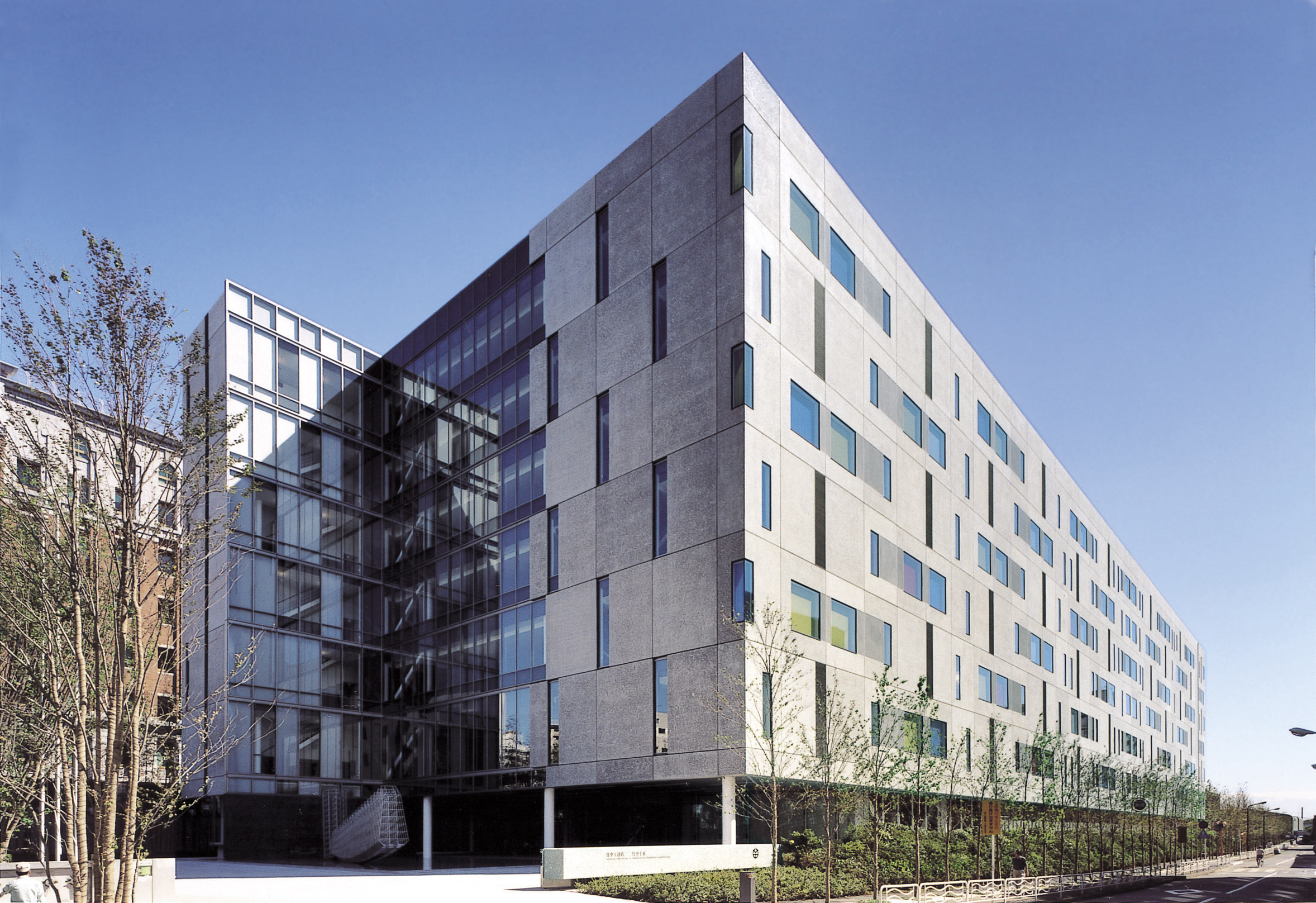
At Takenaka Corporation's Tokyo Main Office, a large office building constructed in 2004, we have achieved a significant reduction in CO2 emissions by installing LED lighting, task ambient + motion sensor lighting, a CO2 control system, as well as solar panels, and BELS certification was obtained in 2021. Actual energy usage has also been thoroughly managed on a daily basis to achieve ZEB Ready status.
Hokkaido District FM Center (ZEB Ready)
When rebuilding of the Hokkaido District FM Center, 100 percent Hokkaido wood was used. In addition to reducing CO2 emissions by about 70 percent compared to ordinary steel-framed buildings, we achieved a “wellness office” that will sustain the health and comfort of users. We efficiently capture and utilize winter solar radiation, and we used simulations to determine the optimal opening positions and sizes for effective natural ventilation. As a result, the building obtained the highest environmental certification, S rank of CASBEE Smart Wellness Office, and ZEB Ready of BELS.
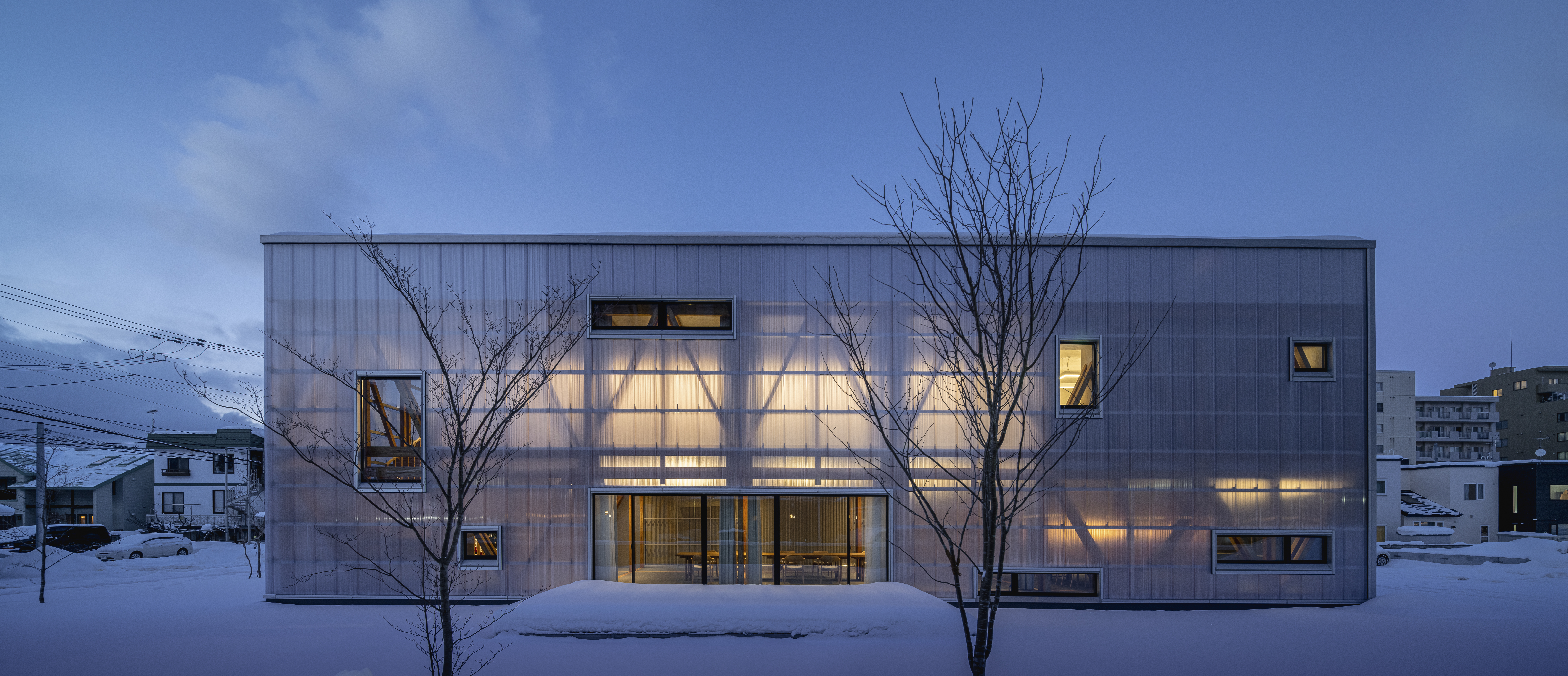
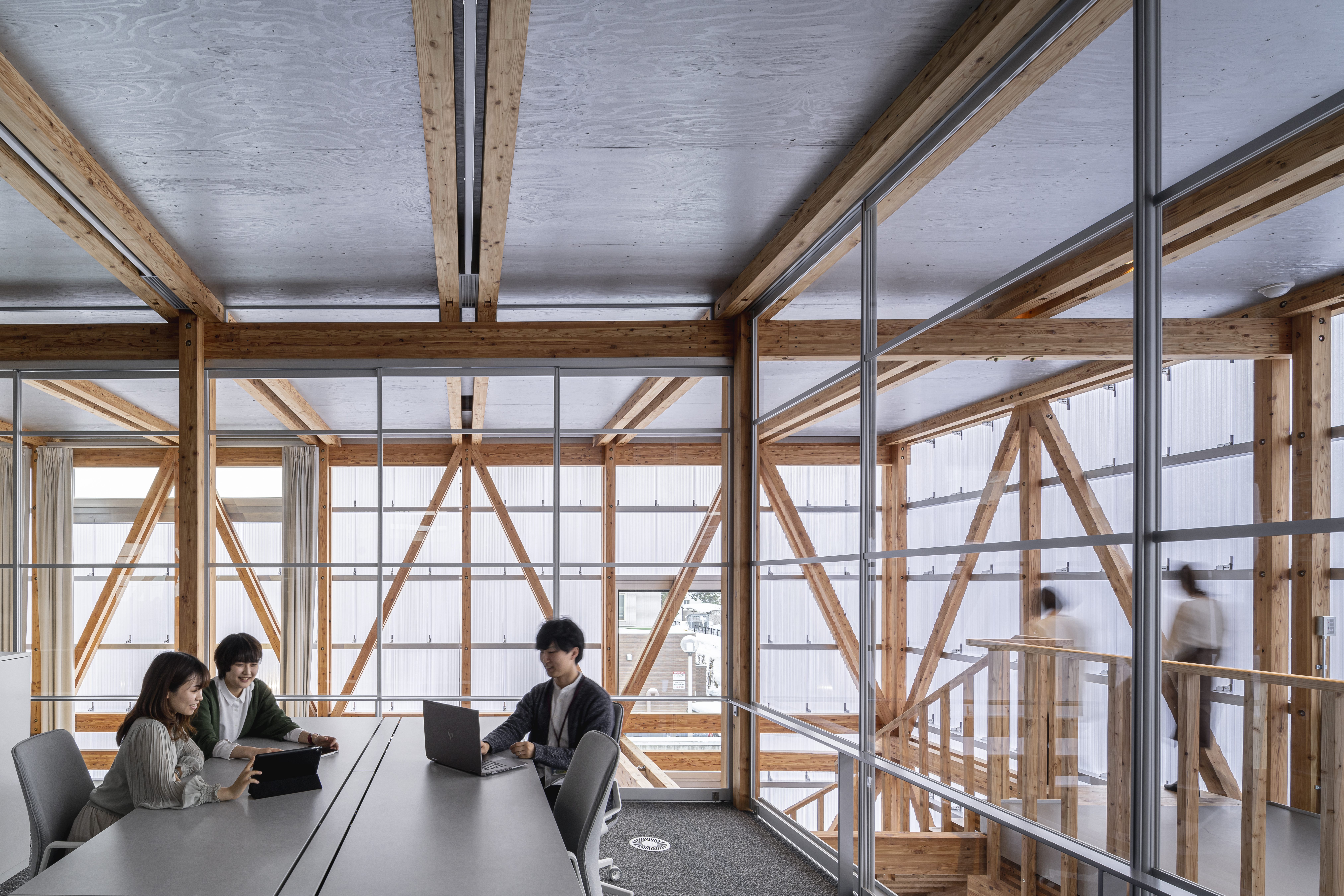
3. Initiatives at rental buildings
At rental office buildings we own, we have also taken steps to reduce CO2 emissions, such as switching to LED lighting in common areas. We aim to further improve environmental performance during renovations and new construction.
Ⅲ. Contributing to customer decarbonization through construction
By reducing CO2 emissions in the entire supply chain, we also help our customers reduce CO2 emissions throughout the life cycle of their buildings.
1. Decarbonizing the building life cycle
CO2 is generated at various stages in a building's life cycle and from various sources: manufacturing of building materials → construction work → customer operation of the building → demolition. We are working to reduce CO2 emissions at all of these stages.
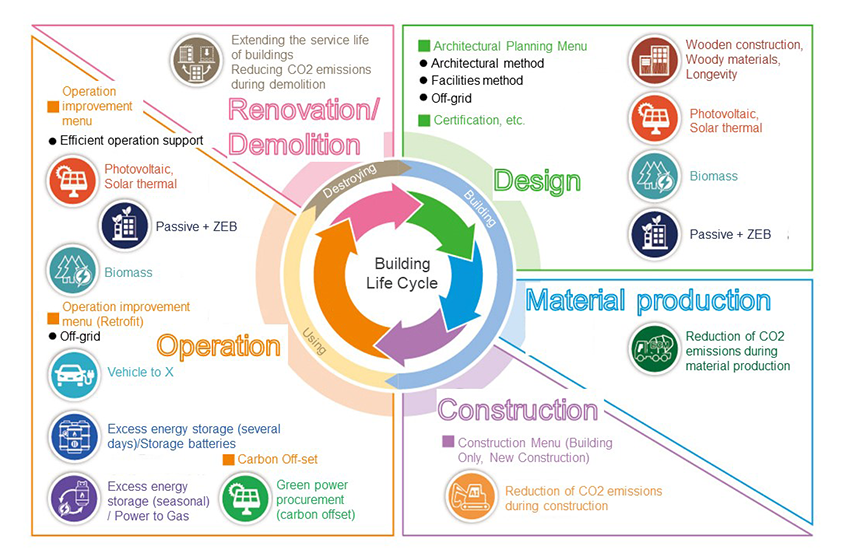
2. Adoption of low carbon materials
In the life cycle of a building, the second largest amount of CO2 emissions after the operation stage is the production of construction materials with most of the CO2 emissions coming from the production of ready-mixed concrete and steel materials (steel frames and rebars). We are working with stakeholders in the supply chain to reduce CO2 emissions related to material procurement.
Adoption of electric furnace steel
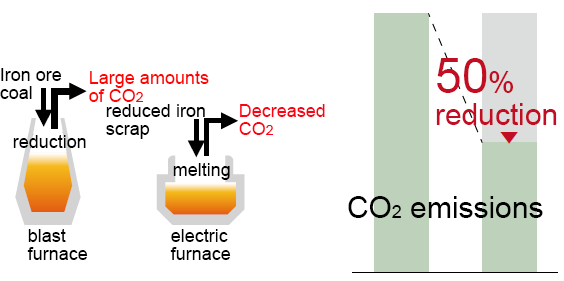
In the process of manufacturing new steel materials, a large amount of CO2 is generated when iron ore is melted in a blast furnace. On the other hand, if steel scrap is melted in an electric furnace and recycled, it is possible to reduce CO2 emissions by about half. In order to ensure the same quality as blast furnace steel, we have established a strict control system and are actively promoting the use of electric furnace steel.
ECM cement/concrete
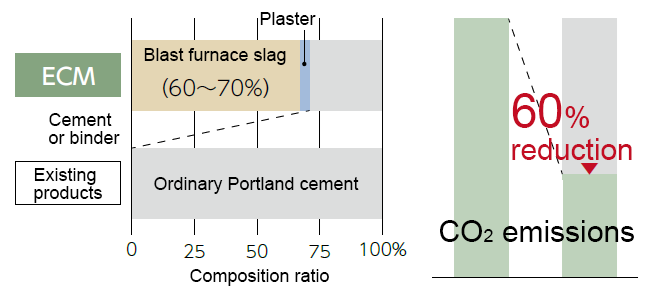
Cement, one of the materials for concrete, generates a large amount of CO2 during its manufacturing process. ECM (energy, CO2, minimum) cement, which we jointly developed, replaces 60 to 70 percent of the cement used in concrete with blast furnace slag, a by-product of steel manufacturing. In addition to expanding its use, we are also working on the development of concrete that has a negative CO2 emissions balance.
Air-conditioning duct made from cardboard Evoludan®
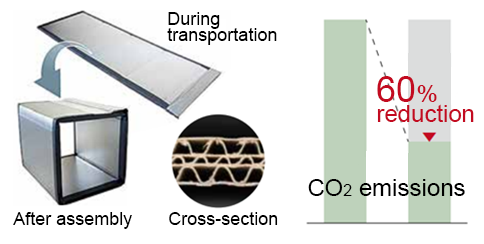
Evoludan is a technology we developed that provides noncombustible performance by covering overlapping corrugated cardboard sheets with aluminum foil. Compared to ordinary ducts that use steel plates, it can significantly reduce CO2 emissions during manufacturing, and because it is lightweight, it also reduces CO2 emissions during transportation (total CO2 emissions reduced by approximately 60 percent).
Active use of wood
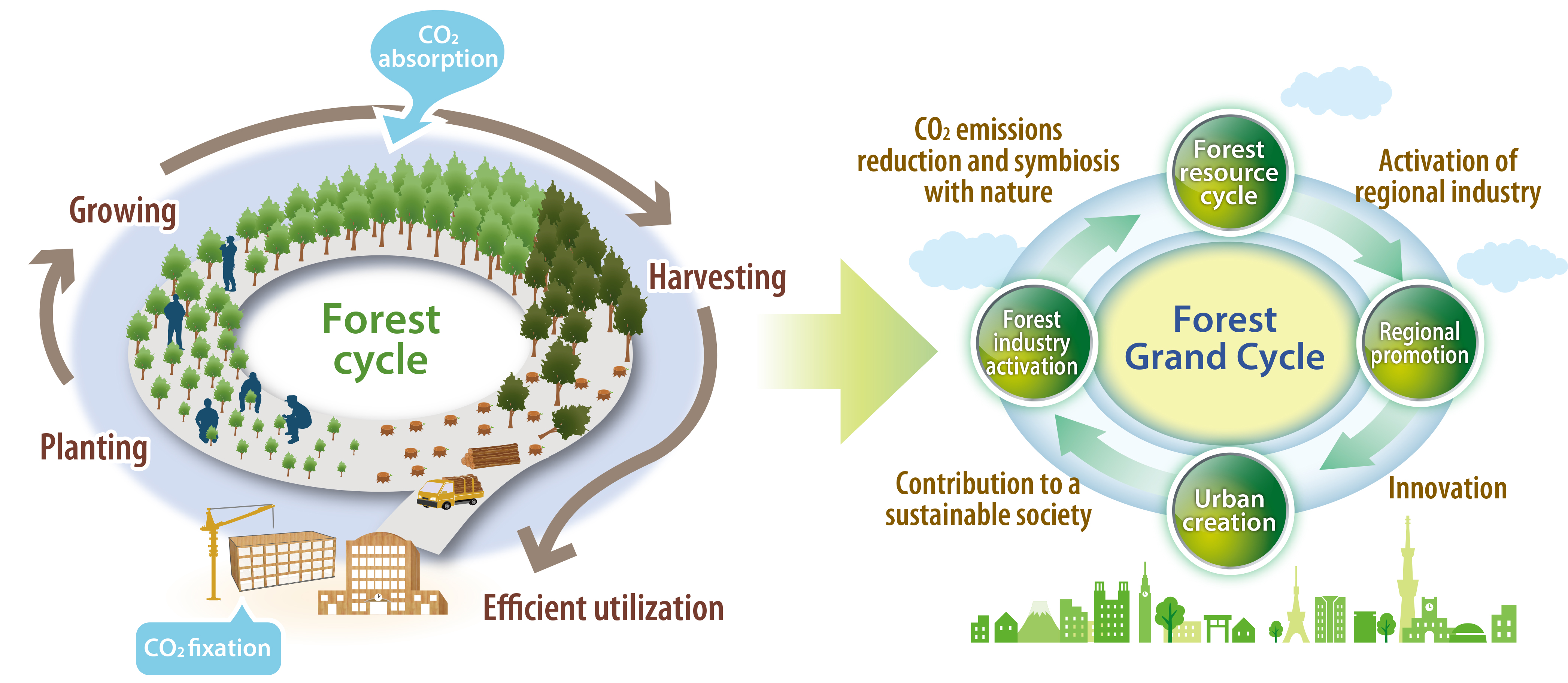
In addition to storing carbon while being used as a building material, replanting trees after harvesting timber encourages the absorption of CO2 by forests, so we expect this to be a measure toward realizing a decarbonized society. In addition to broadening the possibilities of wood utilization with proprietary technologies, such as fire-resistant laminated wood, Moen Wood, we are working to popularize wooden structures and buildings.
In June 2022, we signed an Agreement to Promote the Use of Wood in Buildings with the Ministry of Agriculture, Forestry and Fisheries, and we aim to expand the use of timber by promoting medium- and high-rise wooden buildings and other structures using proprietary technologies, such as our fire-resistant laminated wood, Moen-Wood.
3. Promotion of ZEBs (Zero Energy Buildings)
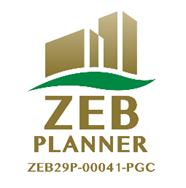
In the life cycle of a building, CO2 emissions are highest during the operation stage by the customer. For the buildings we design, therefore, we actively propose ZEBs (Zero Energy Buildings) and energy-saving buildings in our communications with customers from the early stages of planning. In 2017, we also formally registered as a ZEB Planner, a business entity that provides a consultation service and business support toward realizing ZEBs and discloses those efforts to the public.
ZEB project results
We are expanding ZEB Projects, which are a combination of Net ZEB, Nearly ZEB, ZEB Ready, and ZEB Oriented, mainly with buildings we design and construct. Results since 2009 are shown as a ZEB chart with energy consumption on the horizontal axis and energy generation on the vertical axis.
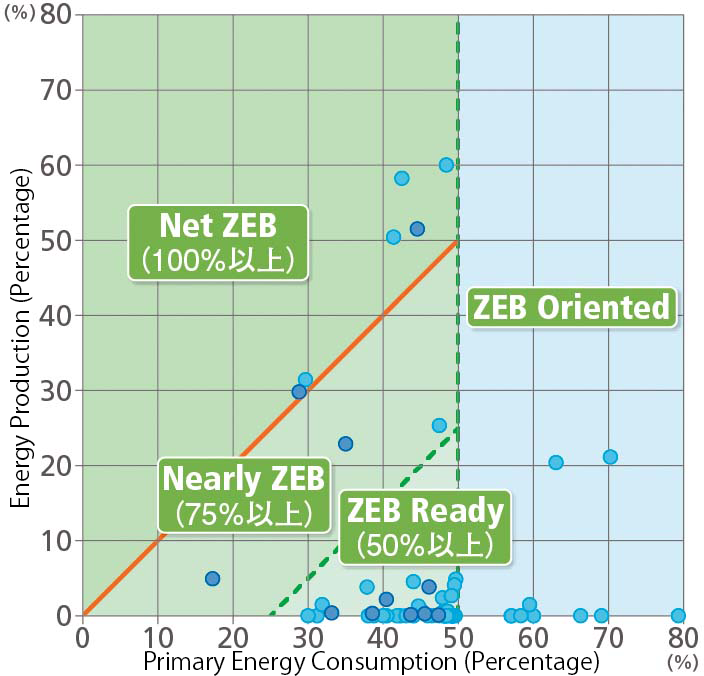
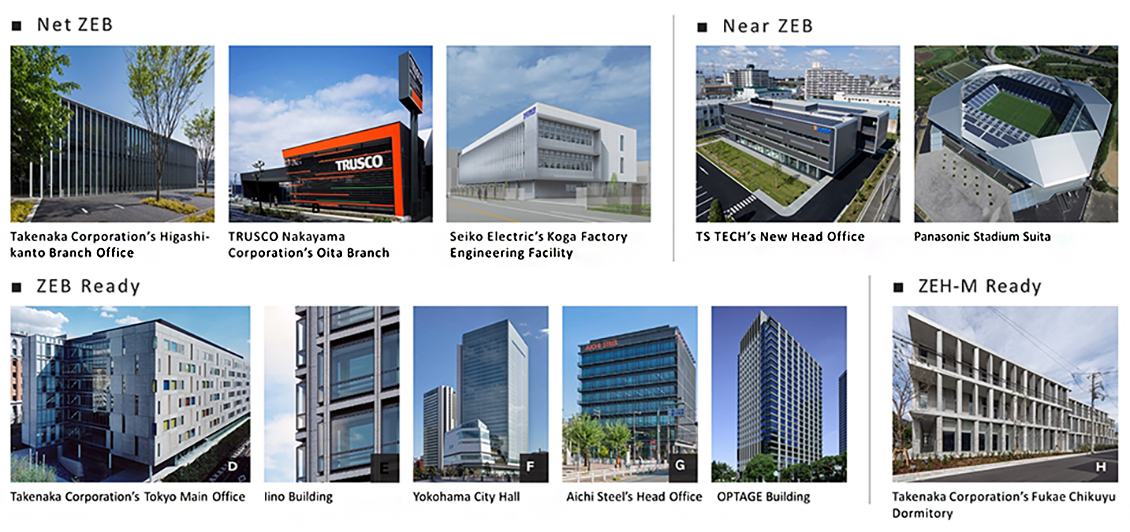
Make ZEBs more accessible®
As part of our initiative to Make ZEB More Accessible®, we are working to achieve ZEBs at an economical cost that is almost the same as that of ordinary buildings.
By providing comfort, economy, versatility, and simplicity, we will contribute to the expansion of ZEBs and decarbonization solutions for more customers.
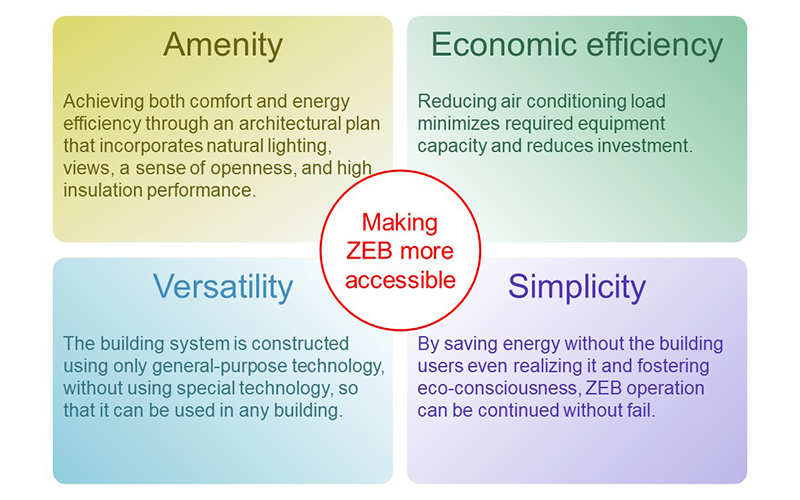
ZEB elemental technology
In order to create buildings with high ZEB and energy-saving performance, we incorporate various elemental technologies into our designs, including those that we have developed. Some examples are improved insulation, reduced air-conditioning loads, and utilization of natural lighting and ventilation.
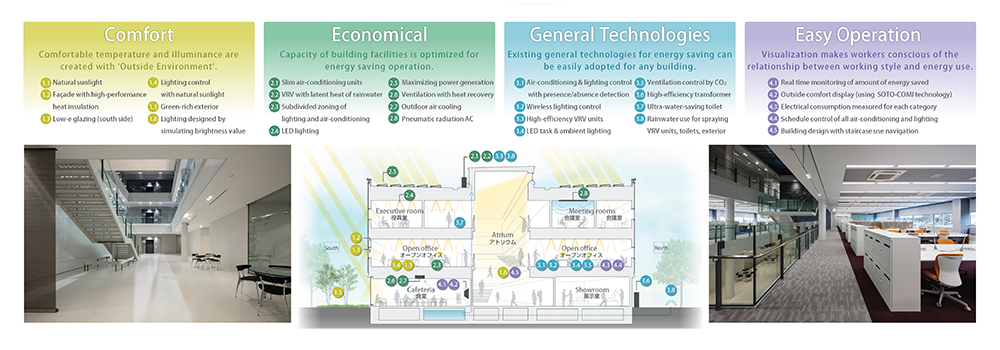
Development of ZEB design tools and preparation of guidelines
We have developed the ZEB design tool ZEBIA (Zero Energy Building Integrated Analysis) in collaboration with an American environmental architecture consulting firm. At the same time, we have developed ZEB Design Guidelines to efficiently design ZEBs, and we started using it companywide in April 2023. By quickly visualizing environmental performance, we are now able to work with customers to create highly energy-efficient buildings from the initial design stage.
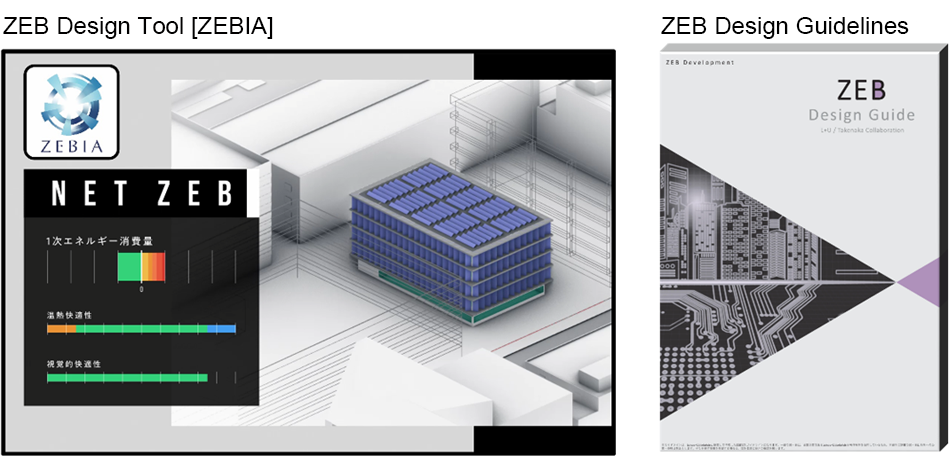
4. Energy management system
Efficient use of energy requires optimal control of various power supply systems, including renewable energy sources, such as solar power generation, storage batteries, and charging/discharging devices for electric vehicles. We have developed our own management system to effectively utilize energy in buildings and contribute to customers' decarbonization through various proposals.
Energy management system I.SEM®
I.SEM, which we independently developed, is an energy management system mainly for small- and medium-sized buildings, and it can also respond to social needs, such as the effective use of renewable energy and power shortages.
I.SEM features
- 1.Energy visualization: Displays real-time information on energy usage and the response status to requests for power savings.
- 2.Power generation/load forecasting: Predicts the amount of solar power generated and consumed, using weather forecasts and actual data.
- 3.PV self-consumption control: Optimally controls storage batteries to fully utilize solar power without any surplus.
- 4.Demand control: Controls distributed power supplies, air-conditioning, and lighting equipment to reduce peak power usage.
Integrated demand response using I.SEM※
I.SEM can automatically control power savings not only for a single building but also for multiple buildings in response to requests for power savings from the power grid. Even in small and medium-sized buildings, by bundling multiple units together, the same power savings as in large buildings can be achieved with contribution to resolving local electricity shortages.
Since 2017, we have been participating in the demand response program run by TEPCO Energy Partner. ●I.SEM® automatically responded to our instructions for power savings in 2017, controlled the power supply equipment in two of our affiliated buildings, and carried out timely efforts toward power-savings.
- Demand response: A system in which consumers respond to requests to save electricity during times of tight electricity supply and demand to maintain a balance between supply and demand.
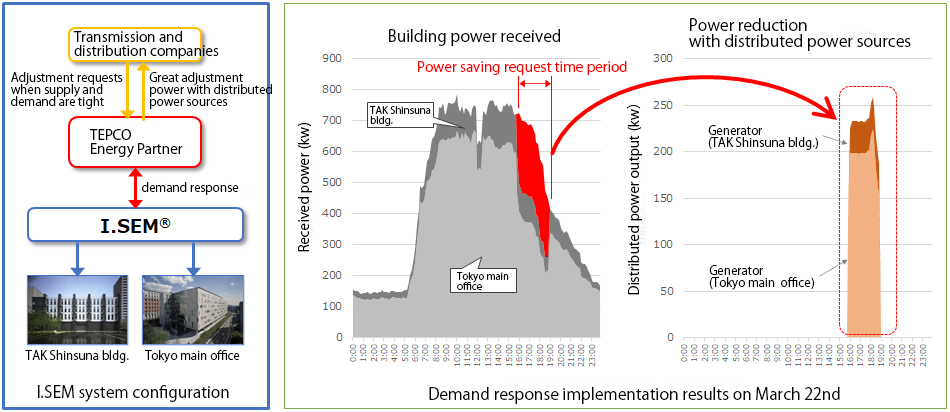
5. Wooden structures and buildings
Trees absorb CO2 from the air through photosynthesis and store it as carbon. Since this CO2 will remain locked in the wood until it is burned, this is also referred to as “carbon storage,” and use of wood is expected to be one of the ways to achieve carbon neutrality. In addition, the use of wood has multifaceted benefits, including revitalization of the forestry industry by promoting use of domestic timber as well as pleasant psychological effects on people from the warmth of wood. We are actively promoting wooden buildings, which use wood for structural elements (frameworks), such as columns and beams, as well as for interior and exterior finishes.
In this area of wooden architecture, we are also working on the development of fire-resistant structural members and other technologies that are essential for large-scale, high-rise buildings in urban areas.
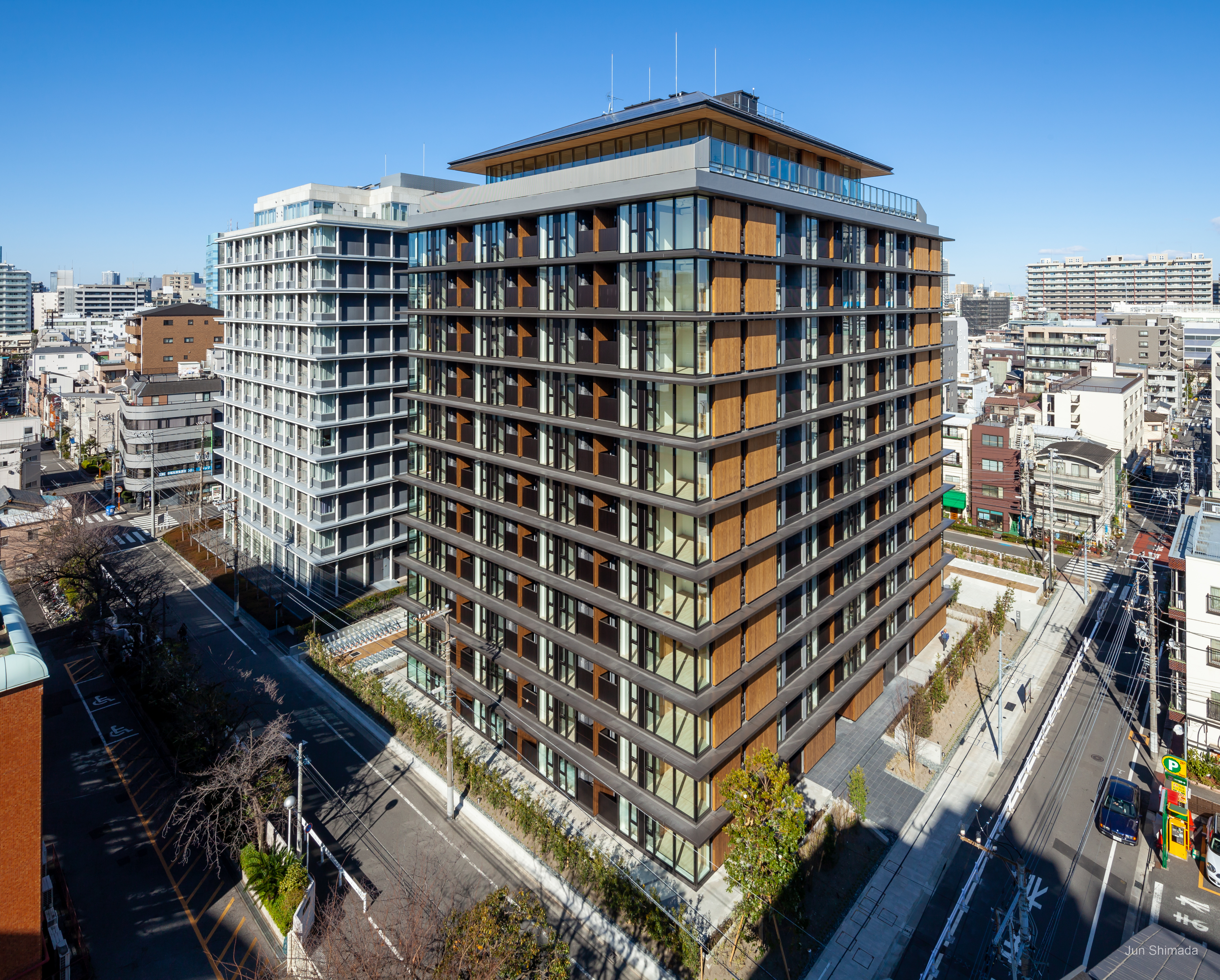
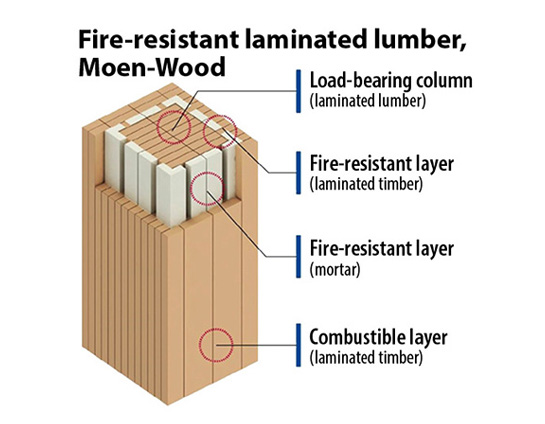
Please refer to the special website for details on this initiative.
6. Operation, diagnosis, and improvement of existing buildings
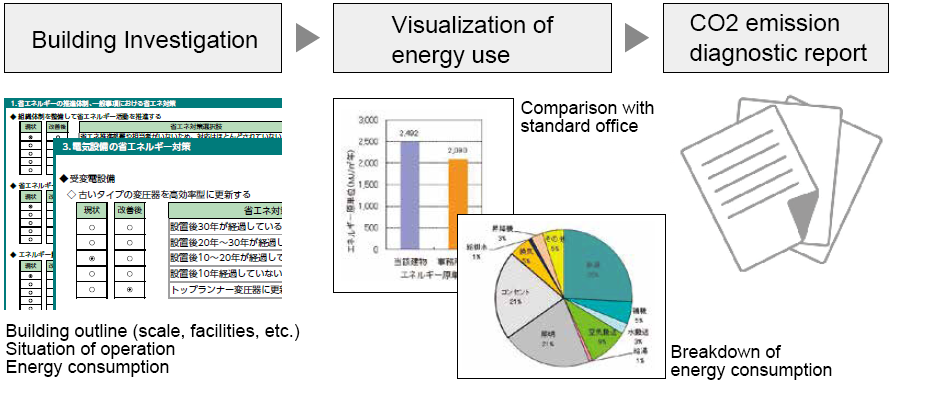
In order to reduce energy consumption during building operation, Asahi Facilities, a group company, makes detailed proposals such as improving the operation of air-conditioning equipment in the buildings it manages. Takenaka Corporation also proposes various decarbonization solutions for existing buildings, such as CO2 emissions diagnoses, operational improvements to equipment and facilities, and renovation work.
Ⅳ. Collaboration in the supply chain
In order to achieve carbon neutrality, it is essential to work together with various stakeholders in the supply chain. In particular, Scope 3 reductions cannot be achieved without collaboration with these businesses.
Development of and popularizing low-carbon concrete
Working together with cement manufacturers, we have developed ECM cement, which can reduce CO2 emissions during manufacturing by about 60 percent, and we are working to expand its application to projects in cooperation with ready-mixed concrete plant operators and others.
Development of CO2 absorbing concrete, etc.
A consortium called CUCO, which consists of 55 companies, universities, and research institutes, has been established and is working to develop technologies, such as carbon negative concrete that absorbs CO2.
Collaboration to expand the adoption of electric furnace steel materials
We have established a circular economy working group for electric furnace steel materials with manufacturers and partner companies, and action is proceeding in this area.
Ⅴ. Technological development that contributes to decarbonization
We are collaborating with other companies to develop low-carbon materials and technologies that will contribute to decarbonizing building operations.
Environmentally friendly concrete that significantly reduces CO₂ emissions - ECM Concrete®
By replacing 60 to 70 percent of the cement with powdered blast furnace slag, a byproduct of steel manufacturing, this concrete can reduce CO2 emissions from concrete by 60 percent.
Noncombustible cardboard duct that contributes to CO₂ reduction and labor savings - Evoludan® -
An air-conditioning duct made of overlapping corrugated cardboard sheets covered with aluminum foil, which enables a 60% reduction in CO₂ emissions during manufacturing and transportation.
Distributed power supply integrated energy management system for a decarbonized society - I.SEM® -
This is an energy management system primarily aimed at small- and medium-sized buildings that responds to social needs, such as the effective use of renewable energy and managing power shortages.
MetaFarm®, creating energy from food waste generated inside buildings
This is a technology that produces biogas from food waste inside a building, and then converts and utilizes it as electricity and heat. It is a recycling system that reduces CO2 and costs from transport and processing by reducing the amount of waste that needs to be carried away.
Highly versatile ZEBs that can reduce operating and management costs -Popularizing ZEBs-
In addition to economically saving and creating energy by using general-purpose technology, comfortable ZEB offices will be created by designing with consideration for views, daylighting, spaciousness, flow lines and lighting.
Ⅵ. Renewable energy supply projects
In cooperation with local communities, we have started a renewable energy supply project that will contribute to local production for local consumption and revitalizing the local economy.
TAKENAKA Okuhida Geothermal Power Plant (Gifu Prefecture)
In collaboration with the local Okuhida Takara Onsen Cooperative Association, we are undertaking a 50kW geothermal power generation project using existing hot spring wells. Power generation began in March 2021, and output has been stable throughout the year. Generation efficiency of more than 95 percent has been achieved, which is at the top of this scale. The electricity generated is sold to the Chubu Electric Power grid under the feed-in tariff system of the Special Measures for the Procurement of Renewable Energy Act. Meanwhile, with the goal of local production for local consumption of energy, a portion of this energy is also used for the cooperative's hot spring supply equipment located in the same facility.
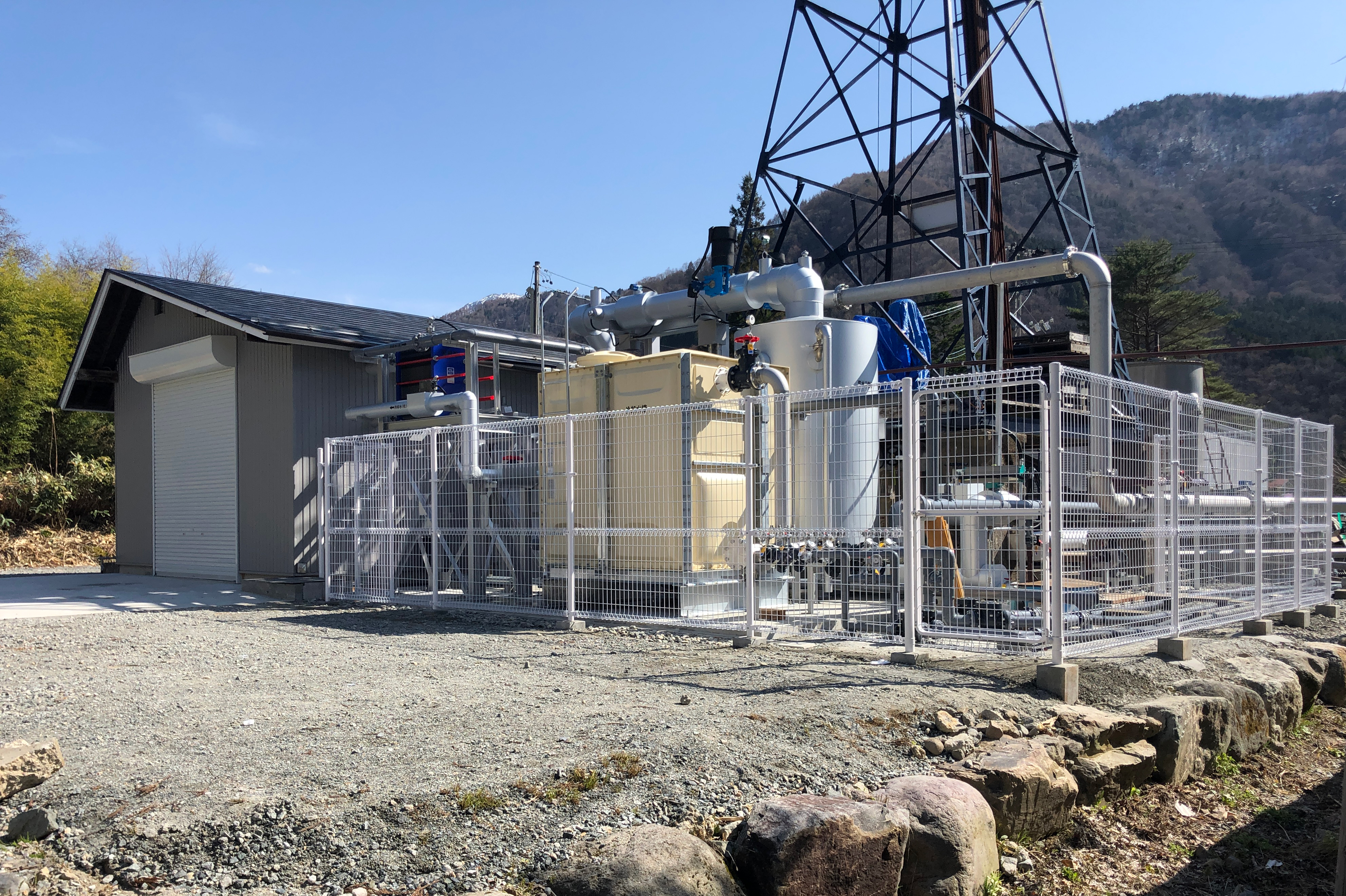
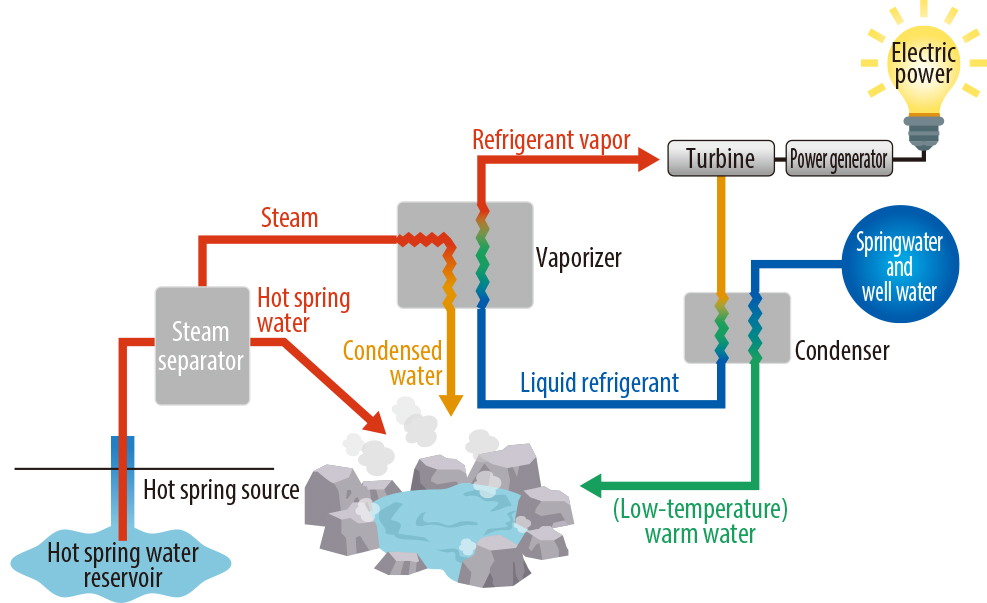
●Uchiko Ryuo Biomass Power Plant (Ehime Prefecture)
Wood pellets are produced from 3,600 tons of unused logs annually after thinning by the Uchiko Town Forestry Association, and these are used as fuel to generate 330 kW of electricity. This is a combined heat and power generation project with the heat from power generation being supplied to two facilities, Auberge Uchiko and Ryuow Fitness Club in the adjacent Ryuo Park in Uchiko Town.
Construction is being financed by local companies and other sources with support from Uchiko Town. By building a wooden structure using locally sourced materials, the aim is to become a leading model for wood biomass power generation projects carried out with local cooperation.
Business operator: Uchiko Ryuo Biomass Energy Co., Ltd.
(Naito Kogyo, Cypress Sunadaya, Takenaka Corporation, Sanyo Boeki, Dainippon Consultants)
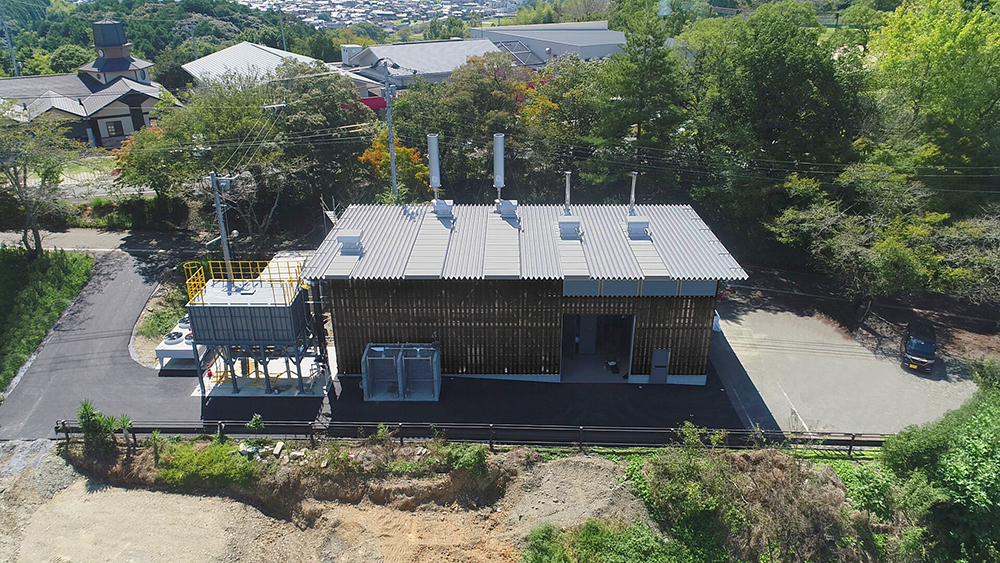