Ensuring quality
Contents
-
Ⅰ. Total Quality Management Basic Policy
Quality assurance that meets customer satisfaction and lives up to society's trust based on our Quality Policy -
Ⅱ. Initiatives for quality assurance, and
providing high-quality, safe construction and services -
Ⅲ. Utilizing BIM to build in quality
- 1. Utilization of data among designers, builders, and partner companies through the deployment of open BIM
- 2. ZEBIA (Zero Energy Building Integrated Analysis)
- 3. Sharing the latest information among related parties and building in quality with StreamBIM
- 4. Deployment of digital construction technology
- Ⅳ. Developing human resources through quality training
- Ⅴ. Customer satisfaction (CS) activities
Ⅰ. Total Quality Management Basic Policy
Quality assurance that meets customer satisfaction and lives up to society's trust based on our Quality Policy
1. Basic stance of “quality management”
At Takenaka Corporation, we define “quality management” as “Earn customer satisfaction and society’s trust through management that persists in stressing quality and challenging the creation of new environments,” which is our Total Quality Management Basic Policy. Furthermore, the “quality” in quality management does not simply mean the quality of buildings, but it also includes the “quality of overall corporate activities” as a member of society. We therefore continue to work relentlessly to improve “quality” and to maintain “quality management.”
- Total Quality Management Basic Policy-
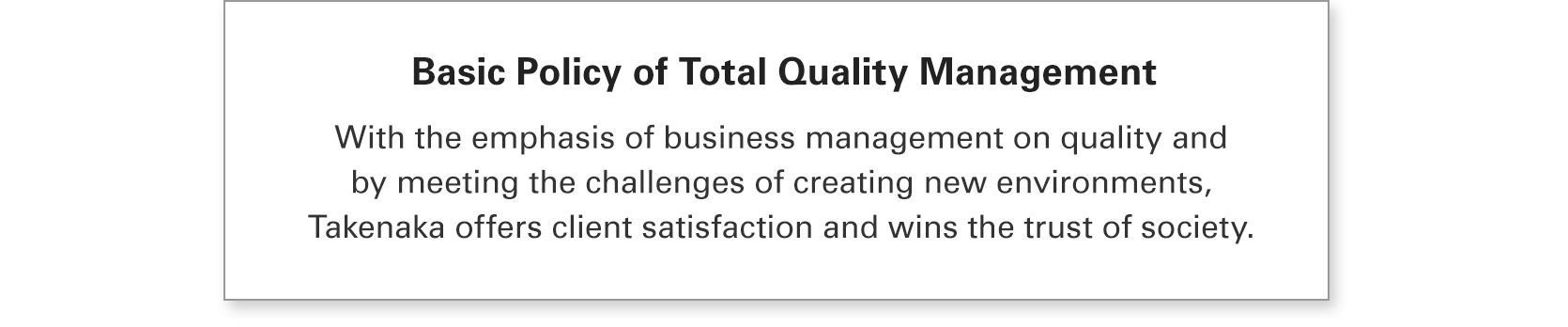
2. Quality Policy
In accordance with our Quality Policy, which is based on our Total Quality Management Basic Policy, we work in unison with our partner companies to promote high-quality architecture that meets customer expectations.
Endeavoring to resolve customer issues, and improving the quality of our works and services
Action Guidelines
- 1.Ensure quality throughout building life cycles from planning to aftercare.
- 2.Create attractive quality by developing and improving advanced technology.
- 3.Implement reliable process management based on our quality assurance system.
- 4.Improve awareness of quality control through continuous education and instruction.
Ⅱ. Initiatives for quality assurance, and
providing high-quality, safe construction and services
1. Building in quality from the design stage, including partner companies
Taking advantage of the merits of our Integrated Design-Build System, we have standardized our workflow as a quality assurance system (ISO9001 certified). By utilizing BIM from the design stage, design, construction, and partner companies can work together to standardize the process of building, thereby ensuring a higher standard of building quality.
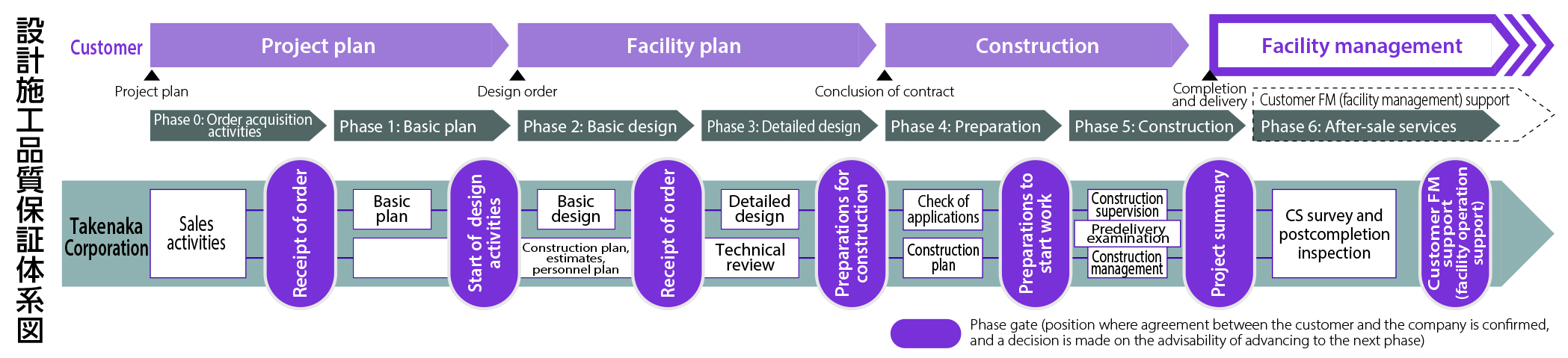
2. Quality management system
Our quality management system (ISO9001: QMS) has been certified for each main and branch office (Eastern Japan, Nagoya, and Western Japan). Based on this system, we deploy activities focused on accurately understanding customer requirements and ensuring their realization through design and construction. We then continually make improvements by turning the PDCA cycle.
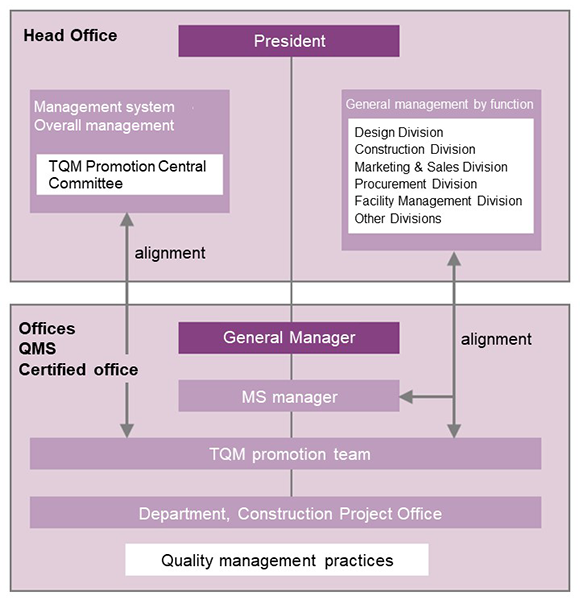
Ⅲ. Utilizing BIM to build in quality
1. Utilization of data among designers, builders, and partner companies through the deployment of open BIM
In order to deploy BIM and build in quality, it is essential utilize BIM software that meets the needs of designers, builders, and partner companies. We are therefore deploying Open BIM based on sharing and coordination in the IFC format, which is an international standard format that does not depend on specific BIM software. In this way, we are building in quality while utilizing data in models from design, construction and cooperating companies from the design stage through to the construction stage.
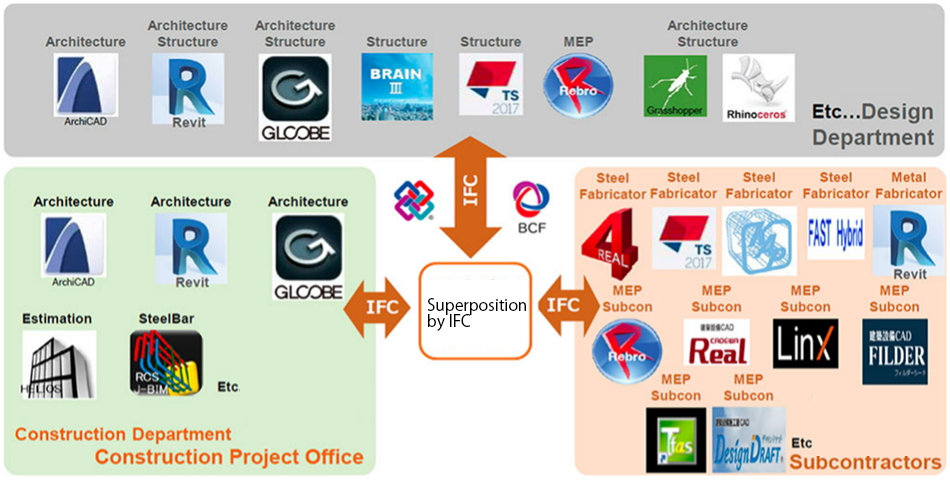
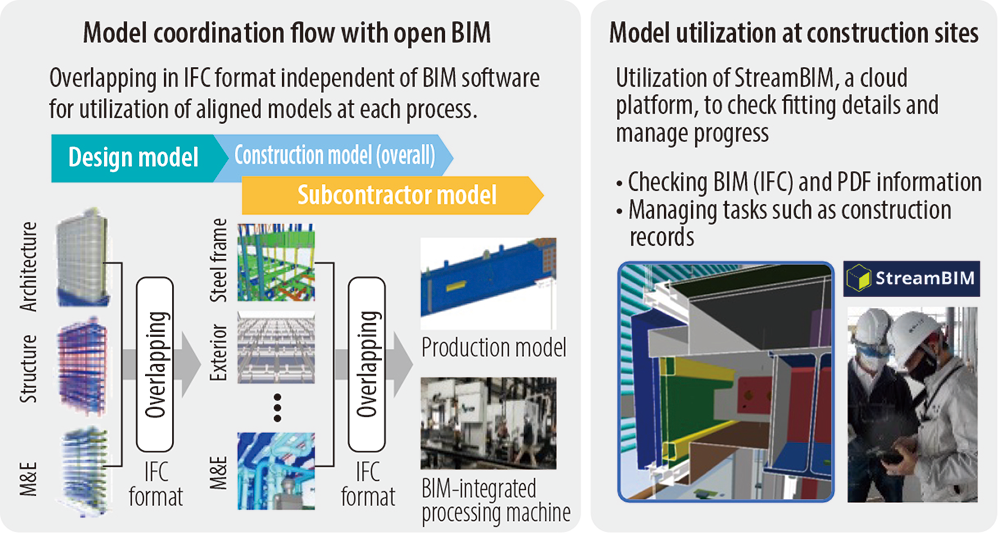
2. ZEBIA (Zero Energy Building Integrated Analysis)
We have developed ZEBIA (Zero Energy Building Integrated Analysis), which is a design tool needed to study ZEBs, which in turn will be environmental indicators for future buildings. This has significantly shortened the time required to verify energy consumption, comfort and other environmental performance, which used to require time in the early design stage. We can also appropriately reflect customer requirements in the design and examine conditions and other matters together with the customer while viewing the simulation results.
As reduction of CO2 emissions is positioned as a quality target for customers, we are seeking to popularize and expand ZEBs in concert with customers, thereby contributing to achieving reduction targets.
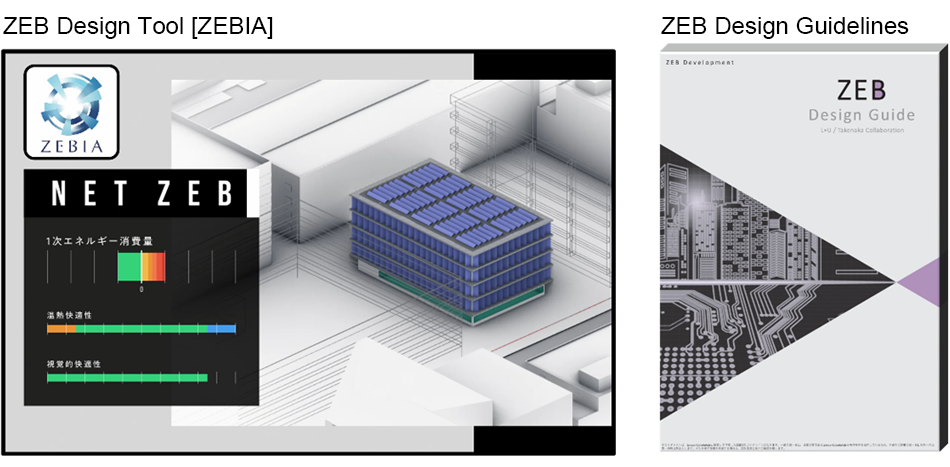
3. Sharing the latest information among related parties and building in quality with StreamBIM
The use of visualized models with StreamBIM, a BIM cloud platform that allows document and workflow management centered on BIM models, provides easy-to-understand information to quickly support customer decision-making, and enable decisions to be made smoothly. With this departure from traditional paper-based operations, we are able to visualize efficient construction management and quality control by checking the site using BIM models, and inputting construction records, inspections and other documents. This allows work to proceed smoothly at construction sites, and quality is also improved. We are also able to digitally check whether construction has been carried out in accordance with the design documents through a “customer-oriented” supervision service, which uses a construction supervision tool that is applied to the system.
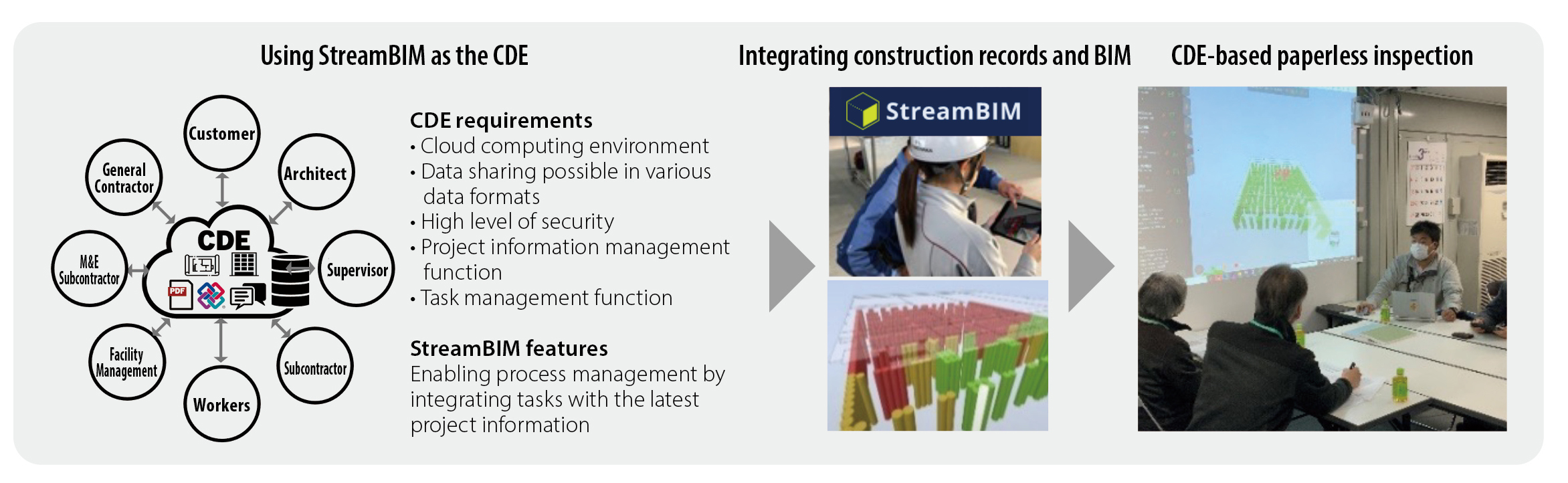
4. Deployment of digital construction technology
Aiming to reform work styles and construction production processes to meet the challenges facing the construction industry, such as a shortage of skilled workers, regulations limiting overtime work, and the digitalization of society, the Takenaka New Production System utilizes digital technology to enhance the value of new construction processes. We will contribute to customer businesses by improving our production capacity to meet their needs, providing construction services, and improving building quality.
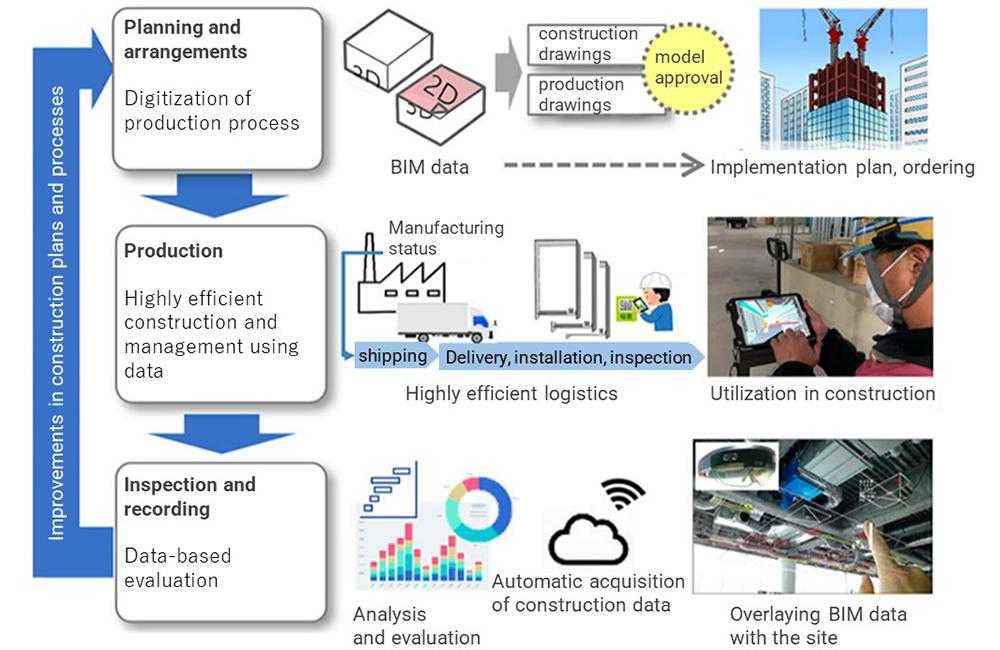
Ⅳ. Developing human resources through quality training
1. Hands-on quality training - Takenaka Practical Technology Training Center Omoi -
In order to ensure quality, it is very important to build in quality based on a quality assurance system. In particular, people involved in the craft of making things are required to practice checking “actual things, at actual places, in real time.” The basic policy of the Takenaka Practical Technology Training Center Omoi is to pass on the process of building in quality to the next generation. In particular, the aim is for participants to master the kata (form) for the craft of making things through hands-on training that allows participants to “see, touch, and experience,” and to cultivate the basics of the toryo (master builder) spirit backed by well-honed sensitivity and knowledge. This allows participants to acquire practical skills and a high awareness of quality.
Omoi implements the following training
- 1. Training for Takenaka Corporation employees
- 2. Training for partner companies
- 3. Training for local communities, students, and others as a social contribution activity
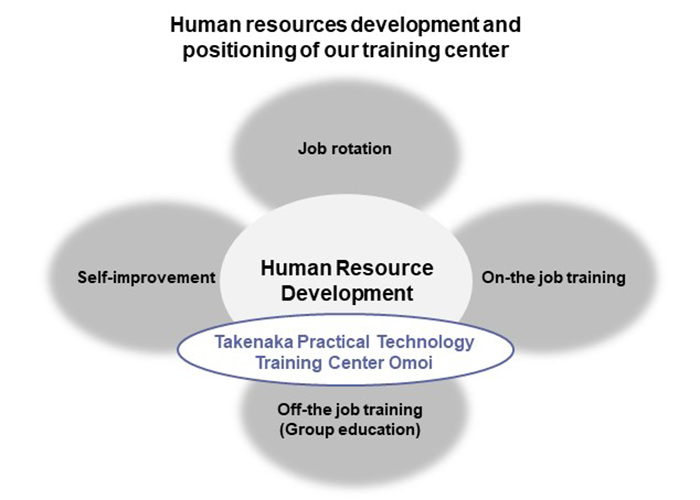
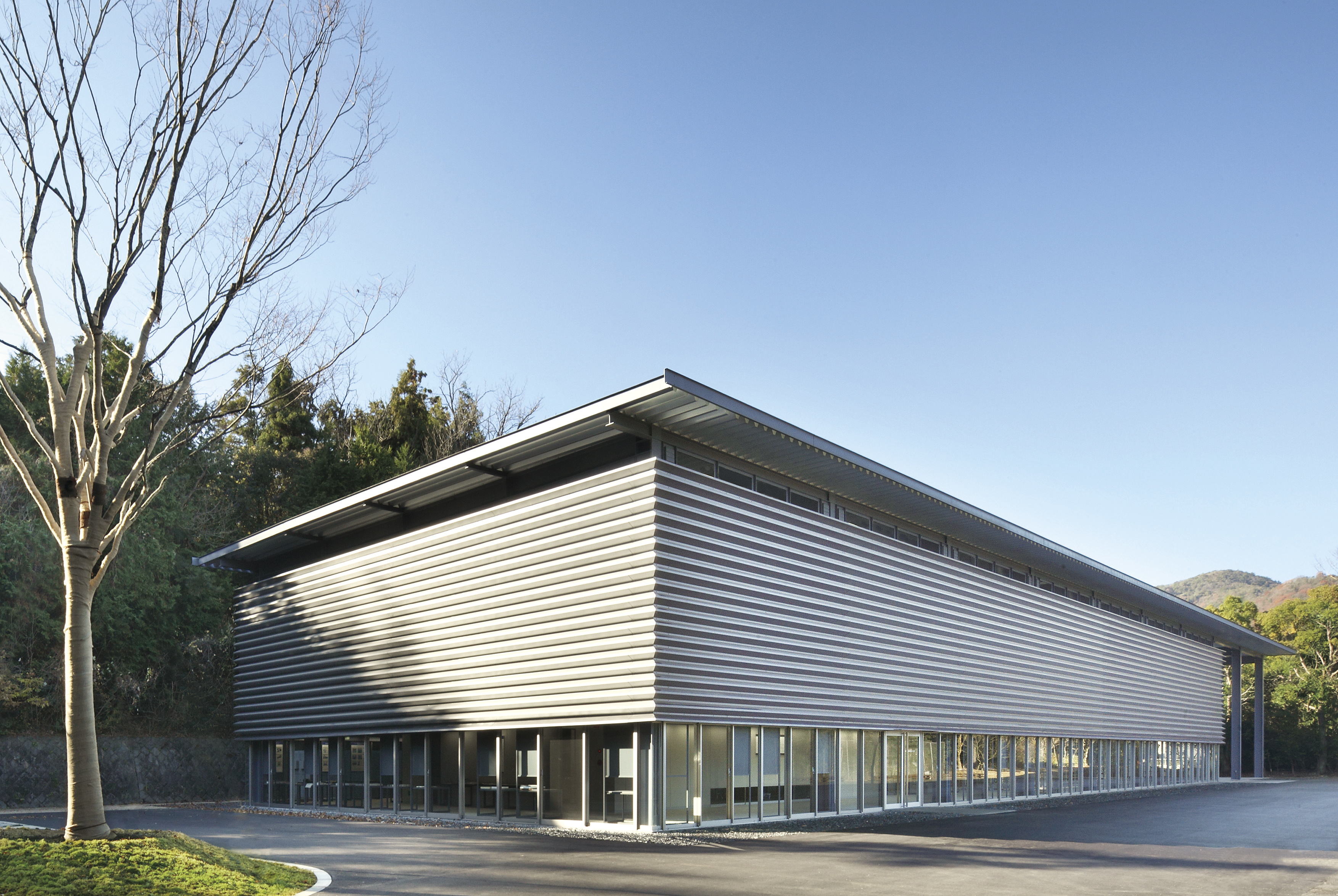
By “seeing, touching, and experiencing” mock-ups, exhibits, and various training sessions, skills for the craft of making things are forged using actual things in actual places in real time. Omoi conveys the accumulated know-how of craftsmen, and passes on their knowledge and skills to the next generation.
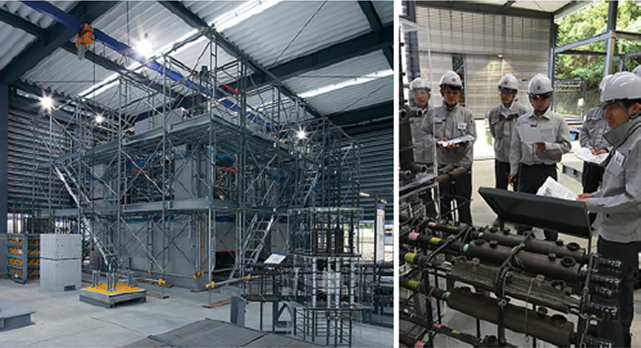
The latest construction method to improve productivity and full-scale model of a connection and joint.
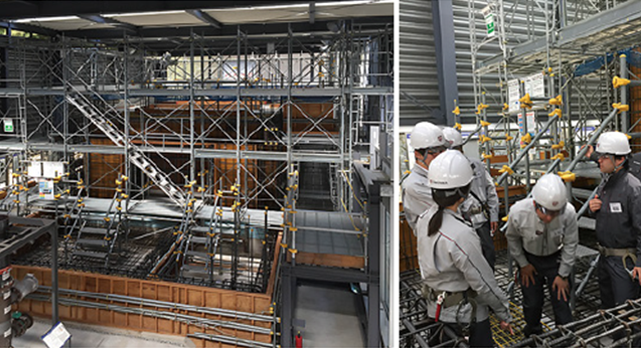
Condominium under construction with mistakes intentionally embedded.
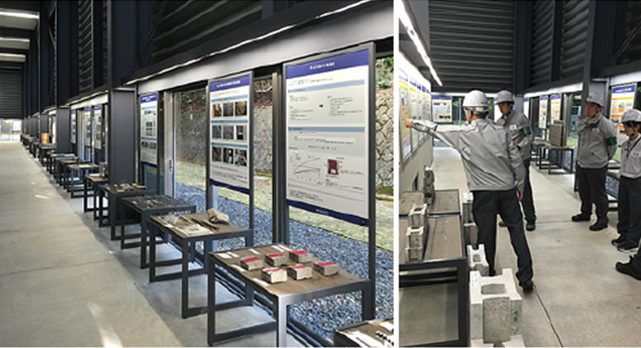
Quality control points for framing, finishing, equipment, and renovation work; and display of actual samples
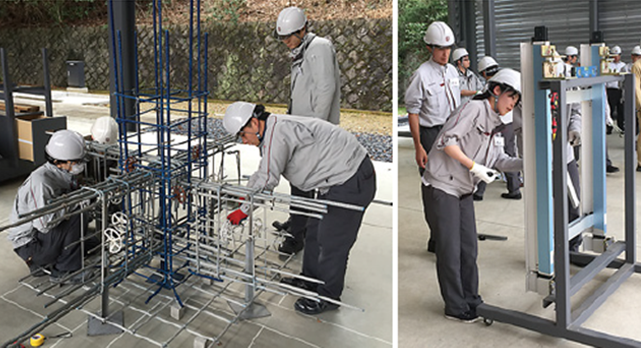
Rebar trials, grouting practice, CW assembly exercise, experiential safety training
Ⅴ. Customer satisfaction (CS) activities
1. Takenaka CS business management system
We position customer satisfaction activities as “activities to enhance our position with customers and society,” and we aim to “build strong long-term relationships with customers.”
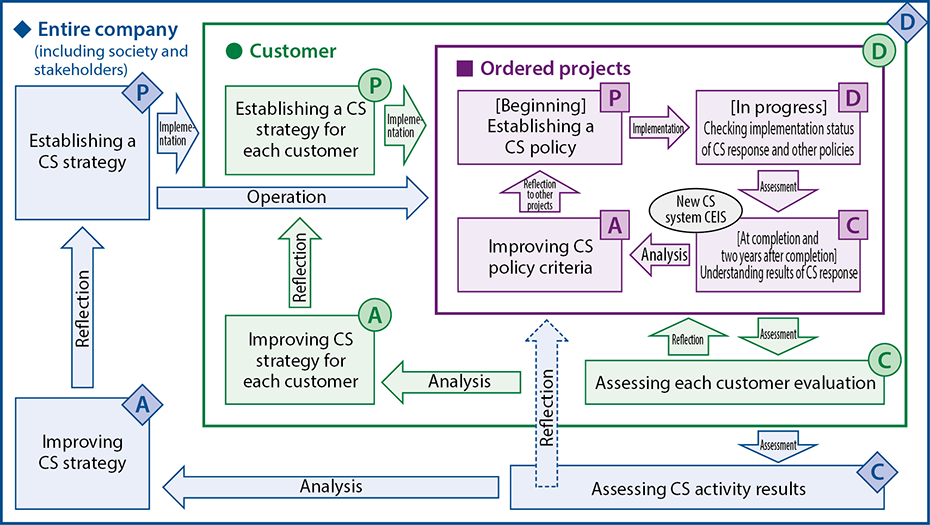
2. Overview of CS survey
We have been conducting customer satisfaction surveys since 1983 in order to improve the quality of our products and services. Just after a building is completed and at the two-year mark, we have designated personnel who visit the subject building to conduct interviews and a written survey on the building itself, the response by our personnel, expectations of our company and other items. We then analyze the results and share them along with feedback to the related internal departments. This is one of the ways in which we are working to improve quality by improving business processes.