Safety and health management
Ⅰ. Safety & Health Policy
1. Safety & Health Policy
Action Guidelines
- 1.Be thorough with safety and health management activities whereby employees and cooperating companies are united.
- 2.Adhere to laws, regulations and internal rules related to workplace safety and health.
- 3.Implement reliable safety and health management based on our quality assurance system.
- 4.Improve awareness of safety and health with employees and cooperating companies by implementing education.
2. Safety Motto
The meaning of safety and health management is to ensure the safety and health of all employees by preventing accidents from occurring in construction activities, based on the basic principle of respect for human life. Takenaka's safety and health activities began in 1927 with the establishment of Takenaka Safety Days and Accident Prevention Guidelines after some soul searching when a derrick collapse resulted in a fatal accident. However, accidents did not disappear, so in 1954 we recommitted ourselves to implementing thorough safety management under the motto, “Safety first in all work.” We have since continued to improve company awareness of safety and taken a variety of measures.
3. Safety and health management system
We have established a Central Committee for Safety & Health Management. Chaired by a vice president, this committee meets twice a year to discuss matters related to safety and health, and the prevention of public accidents. In addition, safety and health management committees convene every month at main and branch offices, chaired by their respective general managers. Discussions are held to ensure the safety and health of employees and workers at construction project offices. In accordance with the company's emergency contact system, information on workplace accidents and injuries that occur while projects are underway are promptly shared inside the company, and follow-ups are conducted when such events occur.
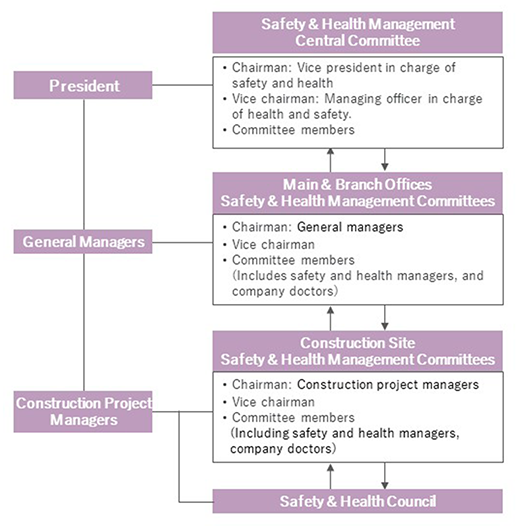
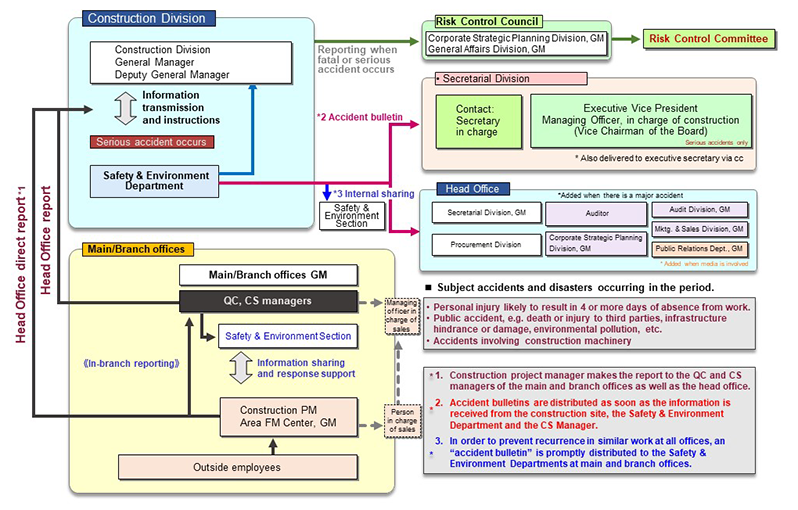
4. Occupational Safety and Health Management System
In January 1928, the same year that Japan's National Safety Week was established, Takenaka's accident prevention activities began with the establishment of monthly Safety Days and Accident Prevention Guidelines. The shop head himself declared, “We are committed to work safety,” and “We will strive to eliminate all accidents from our construction sites in the future.” In addition to the President's Message being issued annually at the beginning of each year and during National Safety Week since 1954, not long after the end of World War II, to express our resolve toward safety management, we have placed, “Devotion to safety activities that are dedicated to a deep love of humanity” as the starting point for our construction activities, and we have established our safety and health philosophy as “safety first in all work.” In order to further solidify this philosophy, we have introduced an Occupational Safety and Health Management System (OSHMS), and we are promoting its operation.
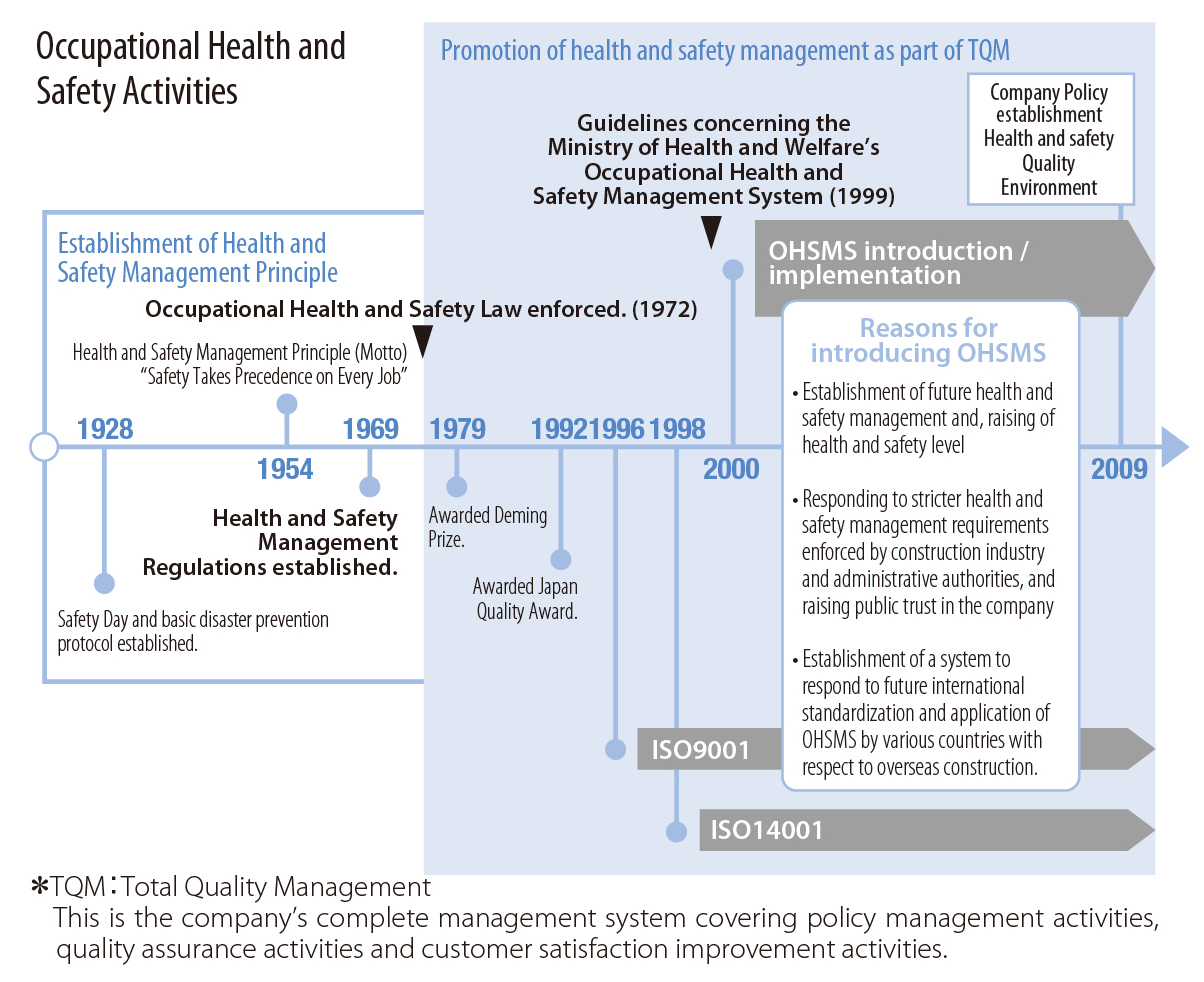
Ⅱ. Safety and health initiatives
In January 1928, we established monthly Safety Days and Accident Prevention Guidelines, and the president himself declared, “We are committed to work safety,” and “We shall strive to eliminate all accidents from our construction sites in the future.” Since 1954, the President's Message has been issued annually at the beginning of each year and during National Safety Week to express our commitment to safety management and communicate this information inside the company and with partner companies.
In 2000, we introduced and began operating an Occupational Health & Safety Management System (OHSMS) in an attempt to embody our Health & Safety Policy, “Realize safe and comfortable workplaces by eradicating disasters and accidents.” In order to achieve our Management Philosophy, we place TQM as the foundation of our management activities. Similar to ISO9001 and ISO14001, OHSMS has been positioned as a system for our safety and health activities that are encompassed in TQM. As a specific current initiative, we are aiming to eliminate workplace accidents by making the prevention of falling accidents our top priority.
1. Ensuring health and safety
Receiving high assessments outside the company for safety and health
On the occasion of National Safety Week, The Minister of Health, Labour and Welfare and the director of the regional labour bureaus present awards to excellent workplaces or companies that have achieved an extremely high level of safety and health performance, and are recognized as a model for others. Our construction project offices received 11 awards in 2023, and a total of 68 awards since 2019. Then in 2021, we also became the first construction company in Japan to receive the Prime Minister's Commendation for Persons of Safety Merits
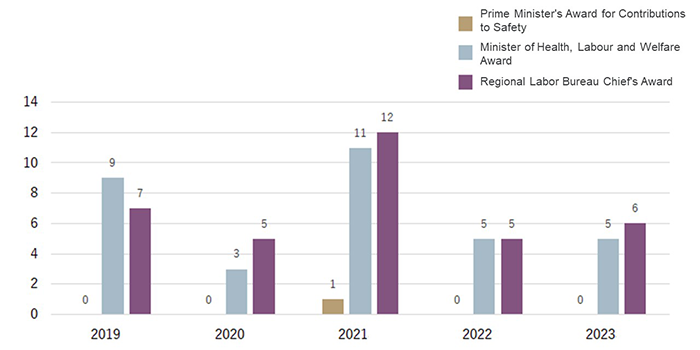
Trends with safety results and frequency rates
The accident frequency rate in 2022 was 0.19, which was a significant improvement compared to previous years, and the number of fatalities at partner companies reached 0.
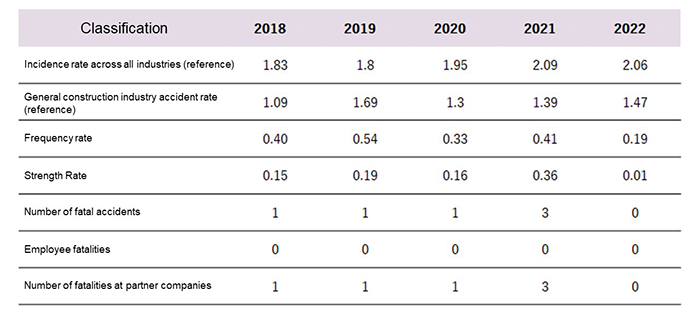
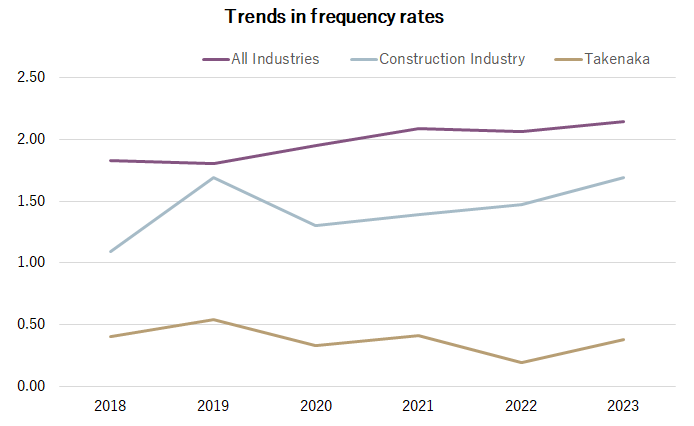
-
Frequency rate: Number of injuries due to industrial accidents per 1,000,000 cumulative actual working hours
All industries and construction industry: 1 or more days off work, our company: 4 or more days off work
2. Education and training
We provide safety and health education to employees and partner companies.
In order to maintain and improve the level of safety and health management in an increasingly diverse and complex working environment at work sites, we are conducting safety and health education, which is focused on trends in public administration and the latest information on safety and health management for employees and persons in charge at partner companies.
We provide employees with the knowledge and know-how necessary for safety and health management through training that is tailored to their actual work sites. This includes basic training by job level and function in safety- and health-related laws and regulations, company rules, duties of chief safety and health officers, preparing plan registrations, and expertise in construction machinery, and electrical equipment.
In collaboration with the Safety & Health Cooperation Association, which is comprised of partner companies, moreover, we are conducting new supplier training, education for foremen and persons in charge of safety and health, specialty education and skills training course for various types of work, and accident prevention training. Then we are also working to raise safety awareness of each and every partner company worker.
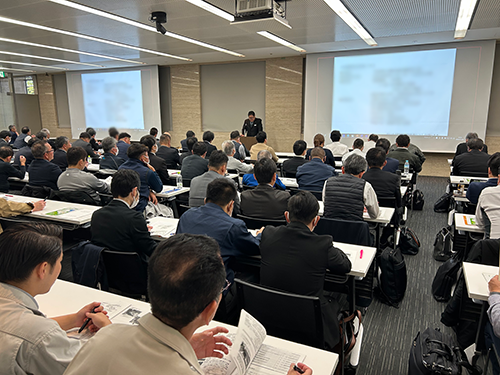
Conducting hands-on safety training that allows students to see, touch, and experience
- Takenaka Practical Technology Training Center Omoi (Hyogo) –
Falls from height and falling over, which can lead to serious accidents, have repeatedly occurred during our construction work. Therefore, we have continued to provide falling accident prevention training annually to young employees, mainly through classroom lectures, but from January 2012, we began a new hands-on falling accident prevention training program at the Takenaka Practical Technology Training Center Omoi in order to hone sensitivity to safety at actual construction sites. By putting a curriculum together that is centered on actually experiencing falling accidents, we are focusing on developing human resources who have acquired the basic kata (forms) of safety management and can apply these in their actual work (Table 2).
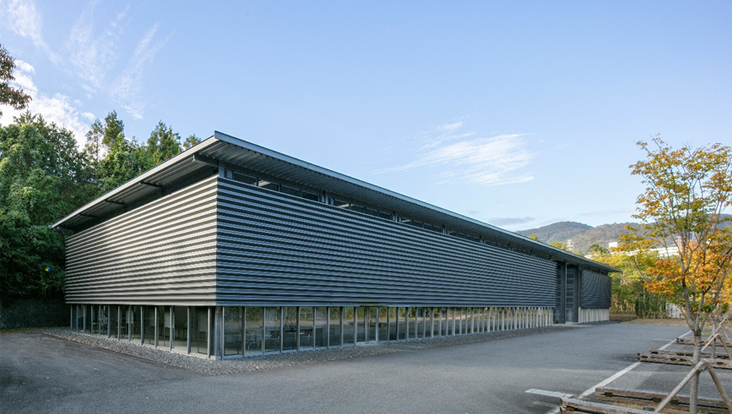
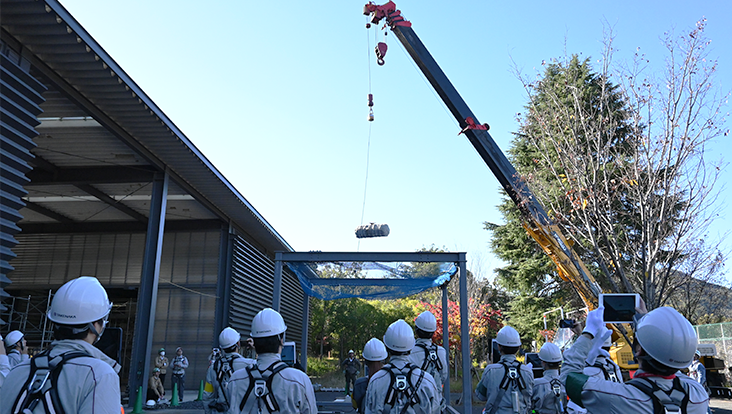
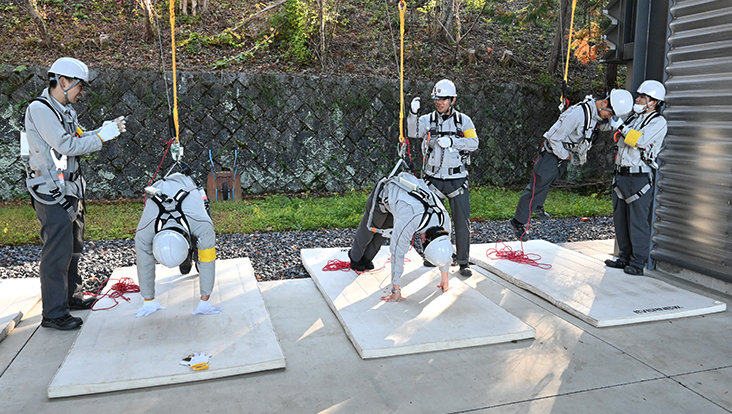
Table 2: Contents of hands-on training to prevent falling accidents
1. Confirmation of falling impact | By dropping a sandbag directly onto the floor from height and experiencing the impact, trainees are able to realize that falling from height can lead to serious accidents. |
---|---|
2. Drop test with lifeline | A sandbag is dropped with a safety belt attached to a lifeline for trainees to experience the effectiveness to the lifeline and safety belt. |
3. Horizontal net drop test | A sandbag is dropped onto a horizontal safety net, which is set up on a temporary stage, for trainees to experience the effectiveness of horizontal nets. |
4. Experiencing hanging by a safety belt | Trainees experience the difference in the burden on the body depending on the position of the safety belt, and they are instructed on the correct method of wearing it. |
5. Scaffolding structure inspection training | Trainees look for deficiencies in scaffolding structures, and learn checkpoints for inspections. |
Promoting preemptive safety planning, and improving the knowledge and skills of a diverse workforce
- Takenaka Practical Technology Training Center Omoi (Hyogo) -
Takenaka promotes uniform safety activities at all branches according to the companywide safety and health management guidelines that are established at the beginning of each year. In order to prevent accidents involving falls from height and falling over, which can lead to serious injuries, we are especially promoting preemptory safety planning by always holding meetings prior to dangerous work as well as performing prior checks of work plans and work procedure manuals that have undergone risk assessment.
In addition, the Tokyo Main Office conducts training for foreign technical interns of subcontractors and group companies at the Safety Active Training-Center (SAT-C), which opened in Shinsuna, Koto Ward in 2016. By improving the knowledge and awareness of a diverse workforce, we are working to make our work sites free of public and workplace accidents.
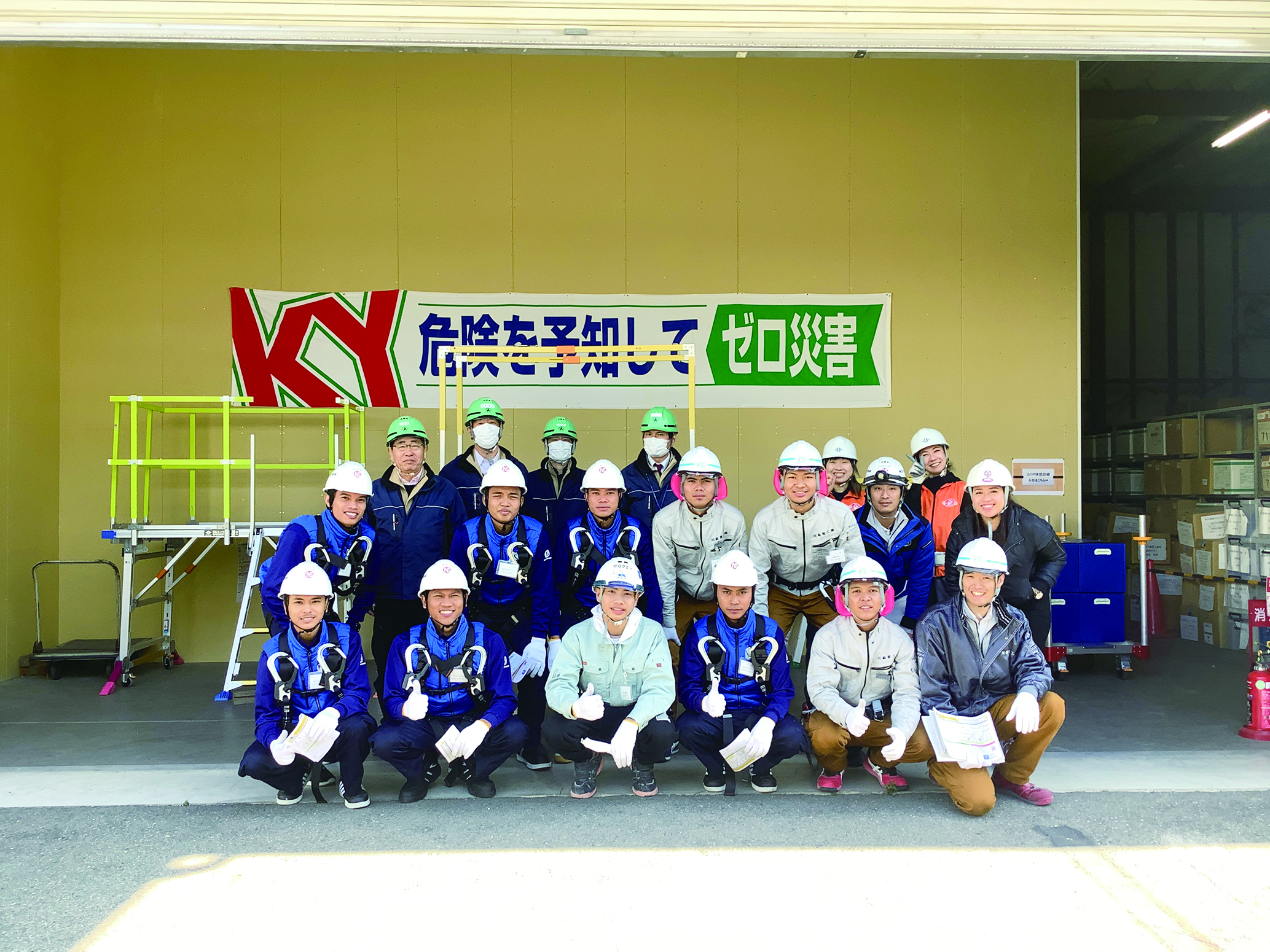
3. Initiatives at work sites
Implementation status of safety and health patrols
In the field of construction work, a building is completed by a main contractor supervising and managing many skilled workers from a variety of specialized construction companies.
In health and safety management, specific risks associated with each construction work are identified in advance, and daily efforts are made to prevent accidents through close communication between our employees and the skilled workers at each partner company. Furthermore, by conducting safety patrols in which internal support departments, representatives of each business operator that employs skilled workers, and the construction project office come together as a united trio, we are focusing on “creation of a work site culture” where everyone can freely exchange opinions. This is how we are working to improve safety awareness. We have also organized safety and health patrols teams made up of female employees to prevent accidents and promote the realization of comfortable workplaces from the perspective of women.
Initiatives to prevent heatstroke
- Health management and preventative measures -
Heat stroke is more likely to occur in hot and humid summer environments. Symptoms can progress from mild to severe in a short period of time and even lead to death. In construction work, there is a lot of outdoor work, including framework erection, and heatstroke is a common occurrence every year, thereby making prevention an issue to be addressed. Before the start of June, when heatstroke occurrences increase, we issue materials calling on construction project offices to take thorough measures against heatstroke. Internal and external personnel work together from both aspects of software and hardware to take thorough measures, which include:
① Installation of large blowers and misting corners, ② Installation of vending machines with sports drinks, etc., and ice machines in break rooms, ③ Wearing protective caps with heat shields or neck guards, ④ Setting break times and hydration times, ⑤ Displaying heatstroke prevention posters, and verbally calling out to check on the physical condition of workers.
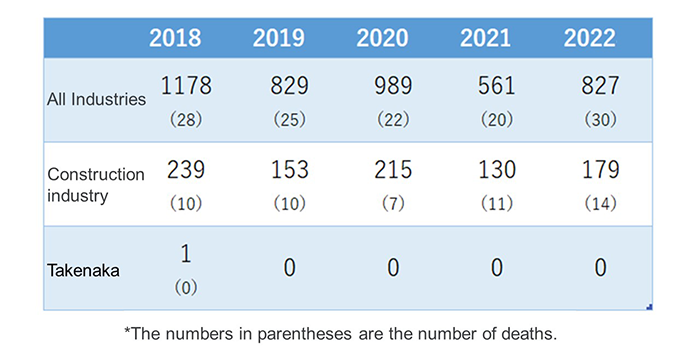
2022 “Occurrence of workplace accidents resulting in death or injury due to heatstroke” (final figures)
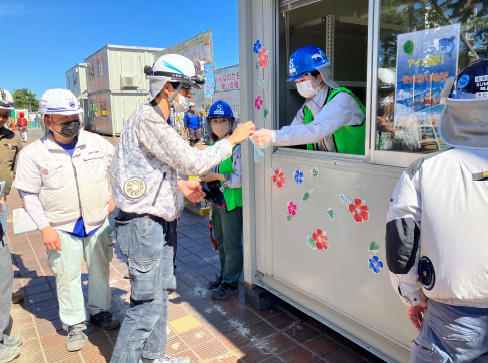
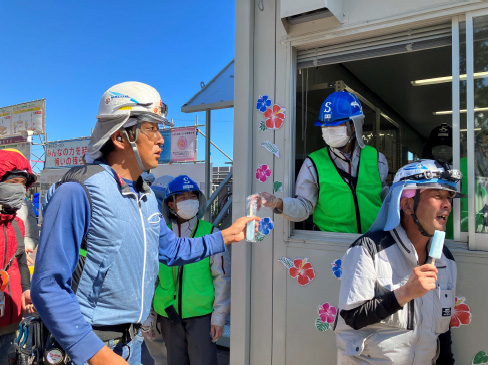
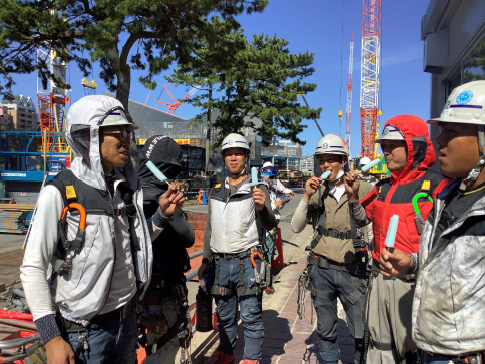
Preventing falling accidents and understanding health conditions
We have positioned the prevention of falling accidents, which occur frequently in the construction industry, and the prevention of heatstroke as priority items in our safety and health management activities.
Falling accidents from heights of two meters or more have been occurring due to safety belts not being used in work that should be done with safety belt hooks or improper hook transition when using double hook safety belts. Then falling accidents from heights of less than two meters, such as falling from a portable workstand, have been occurring due to someone misstepping on a tread when ascending or descending, or falling over from the edge area of floors. Causes have been unsafe behavior due to “unfamiliarity” or “carelessness,” as well as human error due to “misrecognition” or “preconceptions.”
In order to ensure that workers can reliably transition safety belt hooks, we provide training on this during morning meetings as well as training on ascending and descending portable workstands to prevent workers from missteps and falling. We also monitor the health condition of workers by checking their equilibrium from walking on a balance beam at morning meetings because we believe that the daily heath condition of workers is connected to accidents happening as well as the onset of heatstroke. As a result, we have started to see some effect in the reduction of falls from workstands and incidences of heatstroke. We are continuing to steadily carry out these activities into the future.
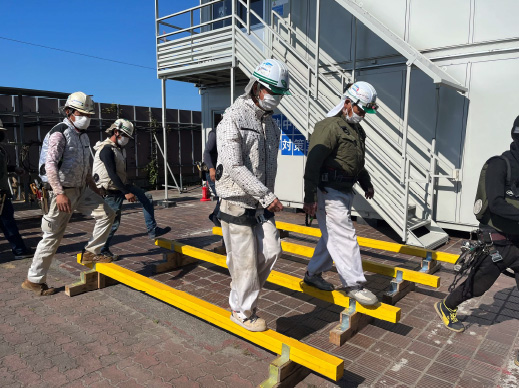
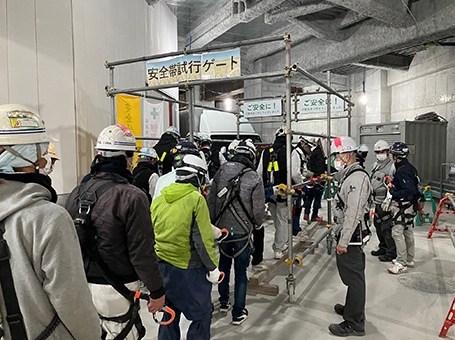
4. Anzen* Information System (AIS)
Sharing safety information using the Anzen Information System (AIS)
Information on workplace accidents that have occurred at Takenaka from 1983 to the present is stored on our intranet, and we have developed the Anzen Information System (AIS) through which employees can freely and easily access, search, and view at any time. Utilizing this system, employees are able to identify dangerous or harmful factors in construction work beforehand and proactively formulate measures to prevent recurrence of similar accidents.
- Anzen means “safety” in Japanese.
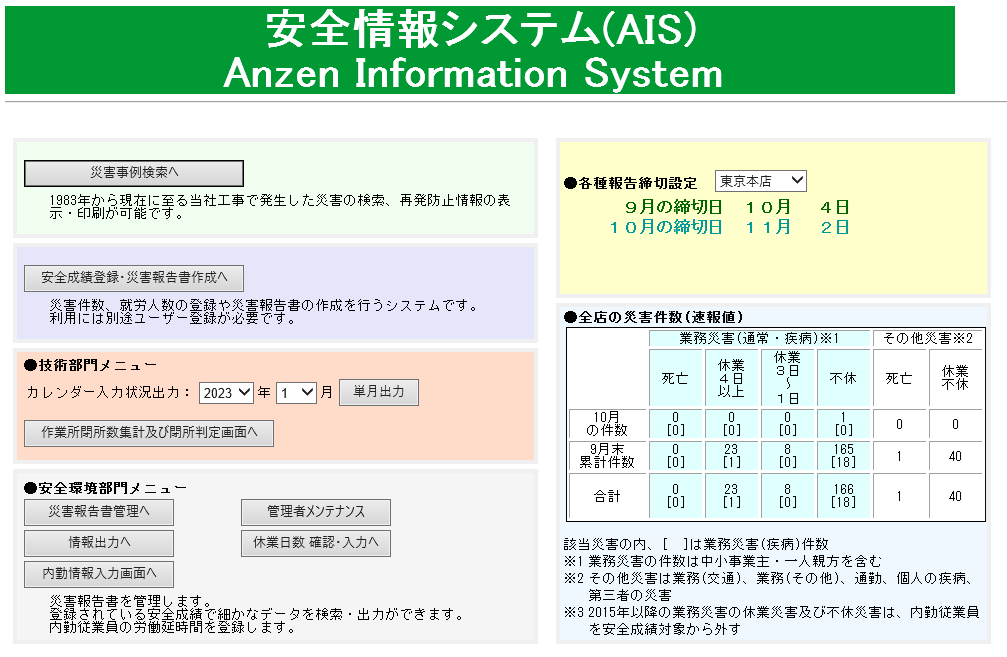
5. SOS [Saigai* Operation System]
SOS [Saigai Operation System] / AI-based preemptive safety tools
AI predicts the accidents that are very likely to occur on a given day at each work site, and then this information is provided daily to the same work sites. At morning, RAKY (risk assessment kiken (danger) yochi (prediction), and other meetings. Accident events that are most likely to occur during the day are shared with the entire work site to be used for risk assessment before work begins. SOS is based on accident information and COMFIRM input data that is accumulated in our AIS (Anzen Information System).
- Saigai means disaster or accident in Japanese.
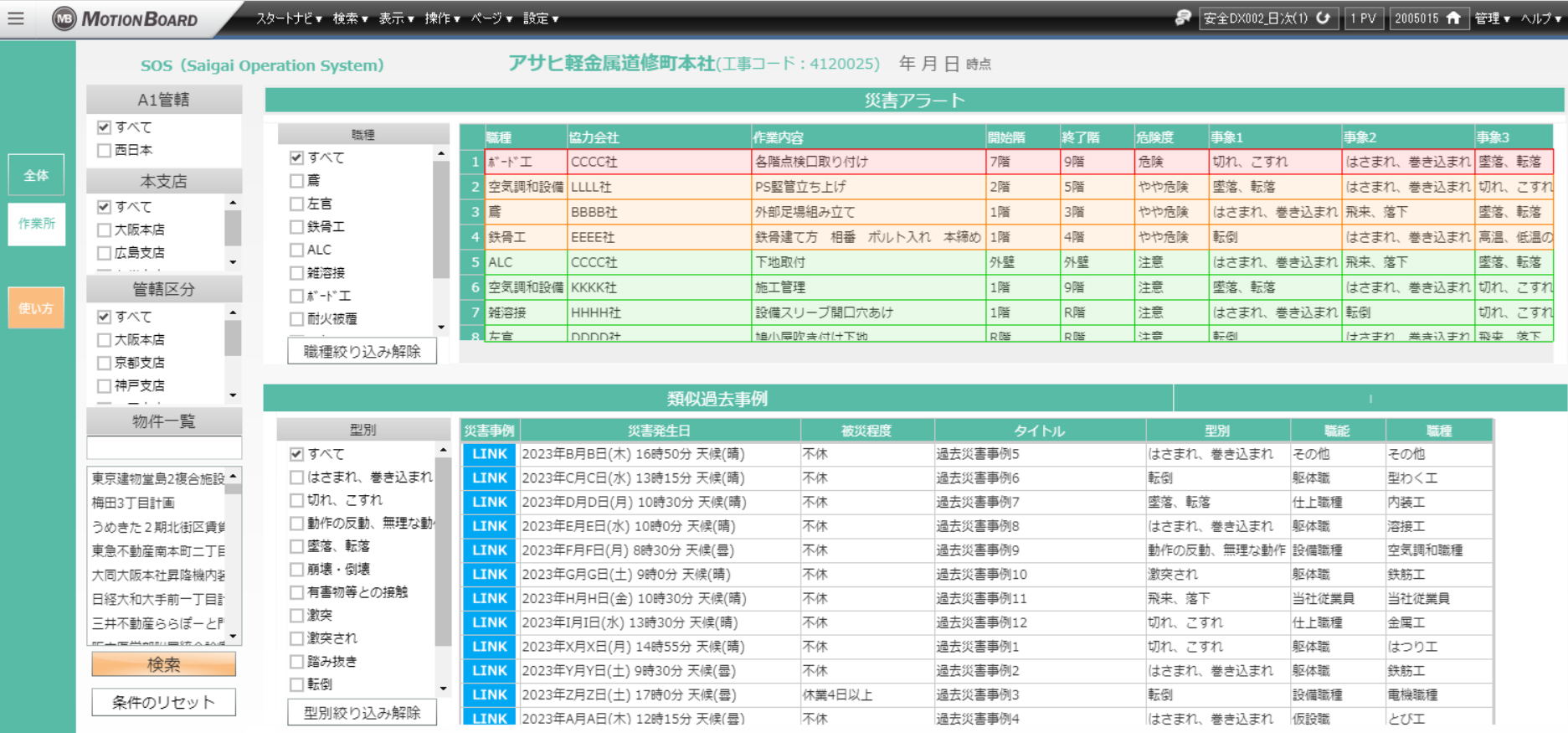