2024年6月7日に竹中工務店が担当する「大阪万博リング西工区」の大屋根リングが上棟を迎えました。2023年4月18日に着工して以来、約1年2か月。まだまだ仕上げ工事などが続きますが、施工責任者と構造実施設計担当者に話を聞きました。
PROFILE (2024年5月現在)
中島 正人
株式会社竹中工務店大阪本店 大阪万博リング西工区作業所 作業所長
1999年入社、2000年から作業所、技術研究所、技術部を経て、2023年より現職。
九嶋 壮一郎
株式会社竹中工務店大阪本店 設計部構造第1部門構造2グループ グループ長
2001年入社、2002年から大阪本店設計部構造部門、設計本部を経て、2021年より現職。
*部署名・役職・インタビュー内容は2024年5月現在のものです。
■万博の施設は閉幕後に解体・リユースされ、その姿はいつまでも残りません。だからこそ、プロセスを記憶として残したい
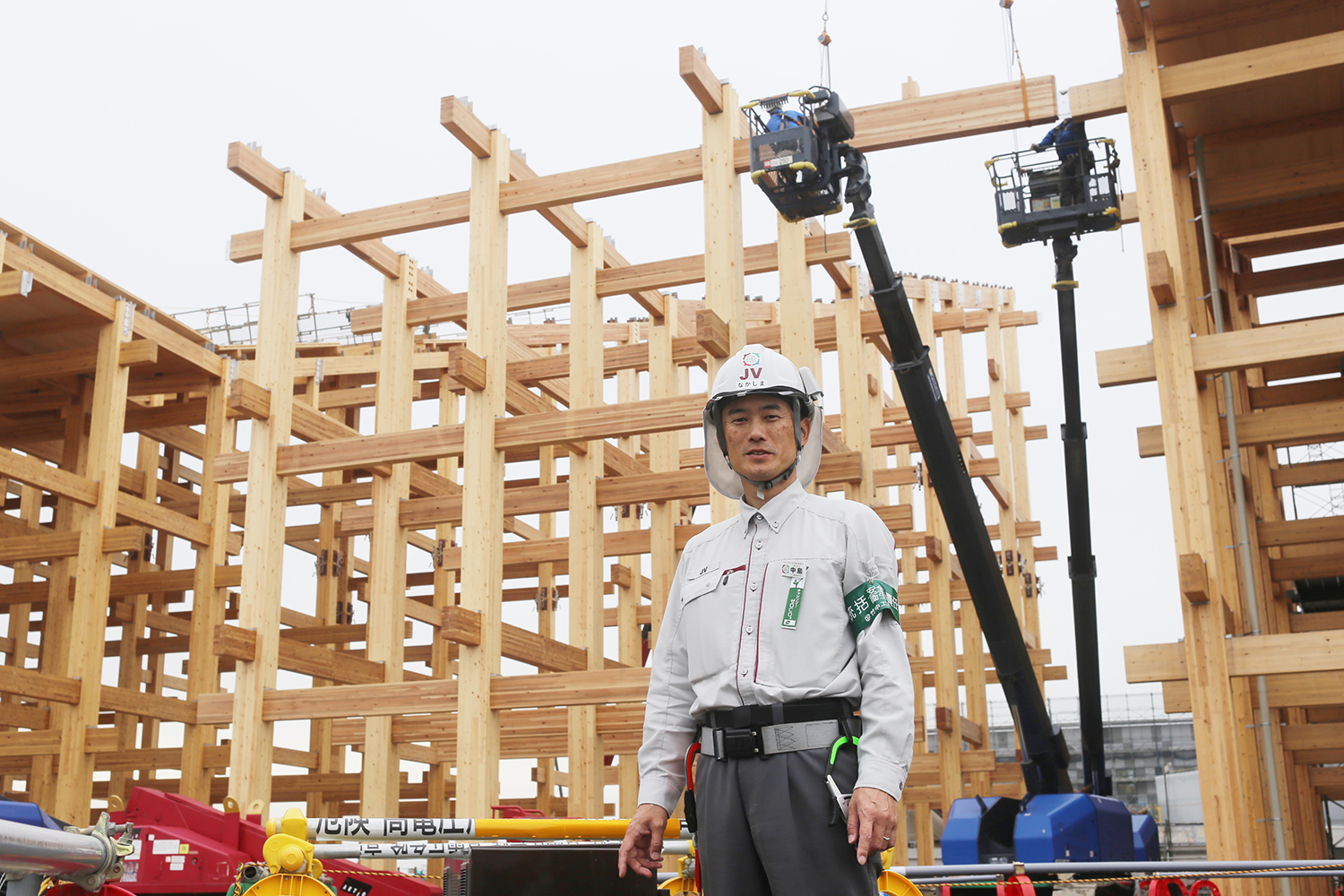
大屋根工事全体の工事責任者として、大事にしていることは何ですか?
中島:「万博の施設は閉幕後に解体・リユースされ、その姿はいつまでも残りません。だからこそ、完成に至るまでのプロセスを大事にして明るい未来につなげたいと思いました。建設プロセスを残す、そして記憶に残すための実験場として、未来の建設業に向けた様々なチェレンジに真剣に取り組むこと。そして一生懸命頑張ってくれているスタッフや職人さん達に感謝の気持ちを忘れないことです。」
この世界最大級の木造建築物に取り組む際にどんな課題がありましたか?
中島:「当時、当社の大阪本店は業務繁忙期であったこともあり、プロジェクトの初期段階では社員が数名ほどしか配属されませんでした。その中で、どうやったらできるかを考えました。先ずは、組織力を活かす。社内の誰を、どの段階で、どう巻き込むか。当社のエンジニアリング力とマネジメント力の融合を試みました。」
中島:「また、国家プロジェクトであるからこそ、工期遅延や事故を起こしてはいけません。そのため、着工までに徹底的な施工計画のつくり込みを行いました。当社工区は他の工区に比べパビリオン等の建屋の密集度が高く、更に工期後半には大屋根リング内側での施設整備工事が集中することが予想されました。大屋根リングを極力前倒しで作り上げることで、リング工事に関わる搬入車両や大型重機が無くなり施設整備工事の作業スペースが確保でき、加えて大屋根下に計画されていた工事搬入経路を早い段階で完全に活用することができます。大屋根リング工事を少しでもスムーズに進めることが、万博工事の全体最適につながると考えました。」
その課題に対しての解決策は何ですか?
中島:「一言でいうと、最新技術を活用して、アップデートした施工とすることです。」
トヨタ自動車の“ジャスト・イン・タイム方式”の考え方を建設現場に持ち込む
中島:「世の中から注目される国家プロジェクトで当社も経験したことがない“世界最大級の木造建築工事“なので、工期遅延や事故が起きないように、工事着工前から考えられるリスクに対して先手を打つ必要があると思いました。具体的には、私が尊敬するトヨタ自動車の大野耐一さんが考え出した、効率よくものをつくる”トヨタ生産方式(ジャスト・イン・タイム方式)“の考え方を建設現場に持ち込もうと。」
中島:「このジャスト・イン・タイム方式を実現するために、日本通運さんと協業※1しました。リングの部材は、柱や梁などの木材部品や金物など、国内外の数十万点におよぶ部品から成り立っていますので、各所との物流管理が重要になります。そこで大阪府堺市の日本通運さんの大型倉庫に部品を集約し、可能な限りそこで部品を組み立てました。屋根がある全天候型の室内で安全かつ効率的に作業を行い、その部材をジャスト・イン・タイムで現場に持ち込みました。」
中島:「この考え方により、工事は非常にスムーズに進みました。」
竹中新生産システム※2の活用
中島:「当社では、お客様ニーズに応える生産力および建設サービスの提供をめざした建築生産変革の取組みとして「竹中新生産システム」を展開しています。ここでは、①生産性向上効果の高い施工計画(最適構工法)の早期検討、➁特定のBIMソフトに依存しないオープンBIM方式※3での効果的な生産準備、③現地工数の削減を目指したオフサイト化の推進(オフサイト ロジスティクス)、④最先端の全自動デジタル加工技術の活用(デジタルファブリケーション)が柱になります。」
中島:「着工前に実際に作業いただく鳶さんの意見を取り入れて考え出した工法を、当社の機材センターで試験施工しました。具体的には施工上の安全性確保と品質確保を目的に、平地での組み立てを行った後に、クレーンで吊り上げるユニット化工法を検証しました。」
中島:「また、木材加工工場との事前検討により、当社から施工BIMデータを支給し、工場での加工機とデータ連携することで、間違いのない、かつスピーディーな木加工が実現できることがわかりました。従来は、木材加工側が独自に機械加工用のデータを作成していましたので、今回のチャレンジによる“デジタルデータをつなぐ”ことにより、真のデジタルファブリケーションが実現しました。」
現代の棟梁として、目指したもの
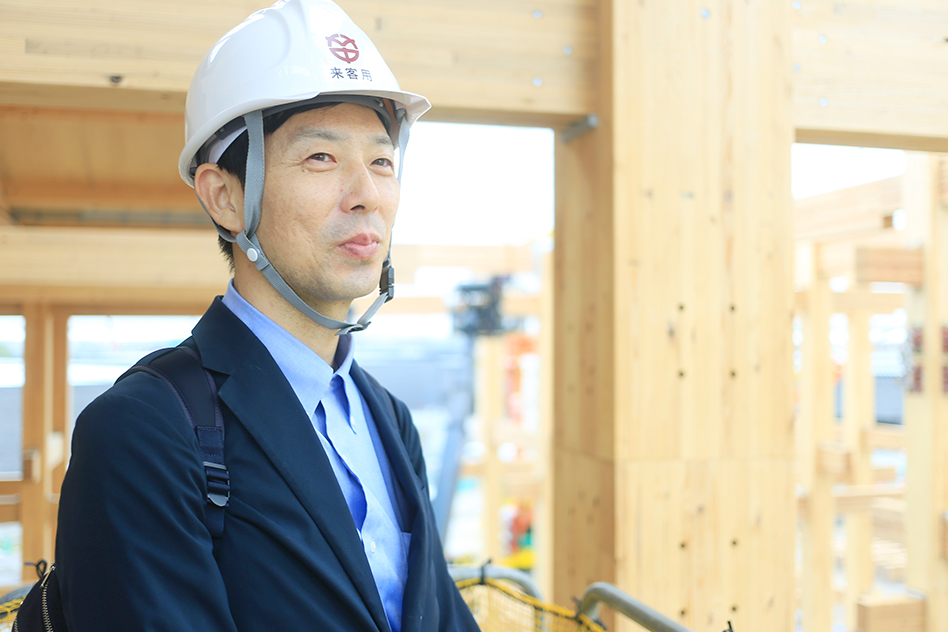
世界最大級の木造建築を担当することになったとき、どう思いましたか?
九嶋:「ビルに換算すると3階建てから5階建ての高さの建物を木造の柱と梁だけで実現する、という今までにないものをどうやったら実現できるかと、新たな挑戦に胸が高鳴るとともに、このプロジェクトを何としても実現せねばと気持ちが引き締まりました。元々、基本設計として伝統的な貫接合という大枠の形が決まっていた中で、構造実施設計者としては、先人の知恵である貫接合への学びをさらに深め、現代の技術で進化することを目指しました。長年の歴史の中で継承されてきたプロポーションや、楔(くさび)により木材が密着するとともに接触幅が増し構造性能が向上するという仕組みを尊重しながら、木材のめり込みを減らす方法を開発しました。技術研究所やエンジニアリング本部とも協業しながらオール竹中で実大実験を重ね、より具体的な形を検討しました。」
順調に進みましたか?
九嶋:「初めてのチャレンジですので、もちろん課題は生じました。何か課題がでたときには、施工サイドの中島とは、自分たちは“現代の棟梁”を合い言葉に議論しました。竹中工務店の創業者は、棟梁です。棟梁は設計もするし、施工もします。立場が違っても、想いは同じです。通常、構造設計の実験に施工者が立ち会うことはないのですが、中島は実験にも立ち会い、今回採用した貫接合の構造上の仕組みも共有し、施工法を検討する際に役立ててくれました。逆に私は、中島が実施した施工試験へ立ち合い、施工プロセスや施工上の課題を共有し、構造設計にフィードバックすることができました。」
施工の立場でのこだわりは?
中島:「一つには、現代の棟梁として、細部にわたる美しさの追求です。例えば、柱のジョイントは隙間を極力なくし、一本の柱に見えるようにするとか、梁のジョイントで必要になったボルトを隠す木栓は、早い段階で取り付けて、梁部材の経年変化と同じにすることで一体感を出すなどの細かい工夫です。」
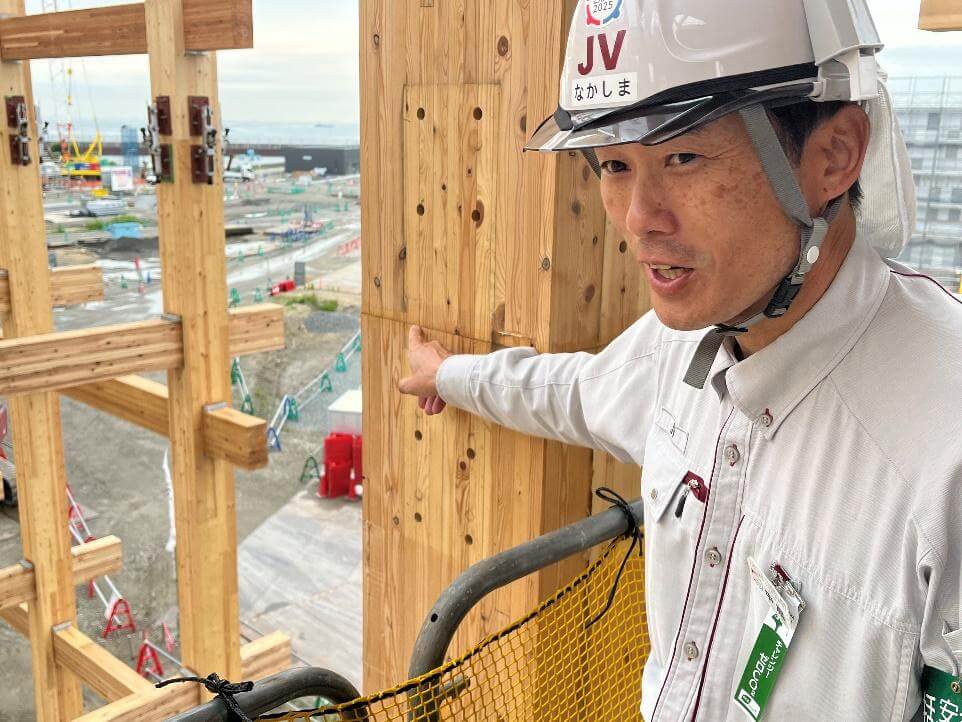
*写真奥の柱は、仮固定用治具がついている状態、手前の柱は完成した状態
九嶋:「一般の方々は、殆ど地上レベルからリングの貫接合を見ることになります。なので、下から見上げた際になるべく余分な部材が見えないように、工夫しています。伝統的な貫工法を尊重しながら、清水寺などでも用いられている貫接合を現代的にアップデートしているわけです」
中島:「部材の建て込みにも、鳶さんの意見を早い段階で取り入れています。ここで作業いただいている鳶さんは、通常、鉄骨の建て込みを得意としています。仕事を安全かつスムーズに進めるためにも、鉄骨の建て込みの方法をリング工事に取り入れました。その方が作業員さんにとって合理的かつ安全に進められると判断したからです。」
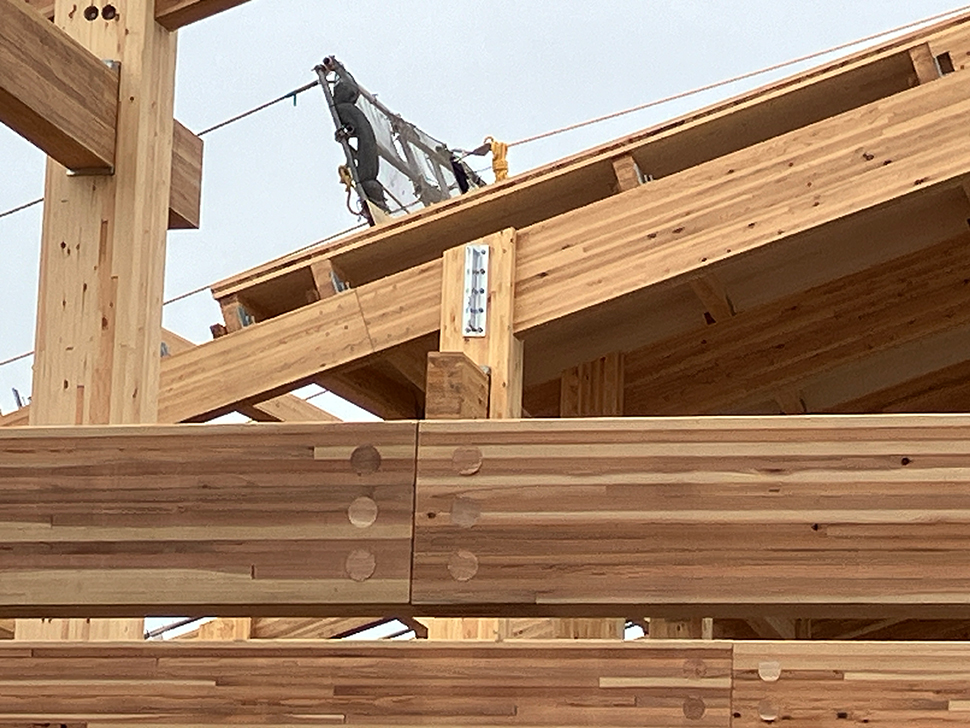
中島:「また、一旦組み上げた部分の木材の劣化等を防ぐために様々な工夫をしました。先ずは木部材に傷をつけることにつながる足場を設置しない無足場工法を実現したことです。次に木材は雨に弱いことが事前検証によって判明していました。そのため、リングの主架構が出来上がると直ぐに膜屋根工事や樋工事をタイムリーに行い、雨から木材を守る配慮を行っています。万博が始まって、こんな部分に気が付く人は少ないと思いますが、“現代の棟梁”としてこだわりました。」
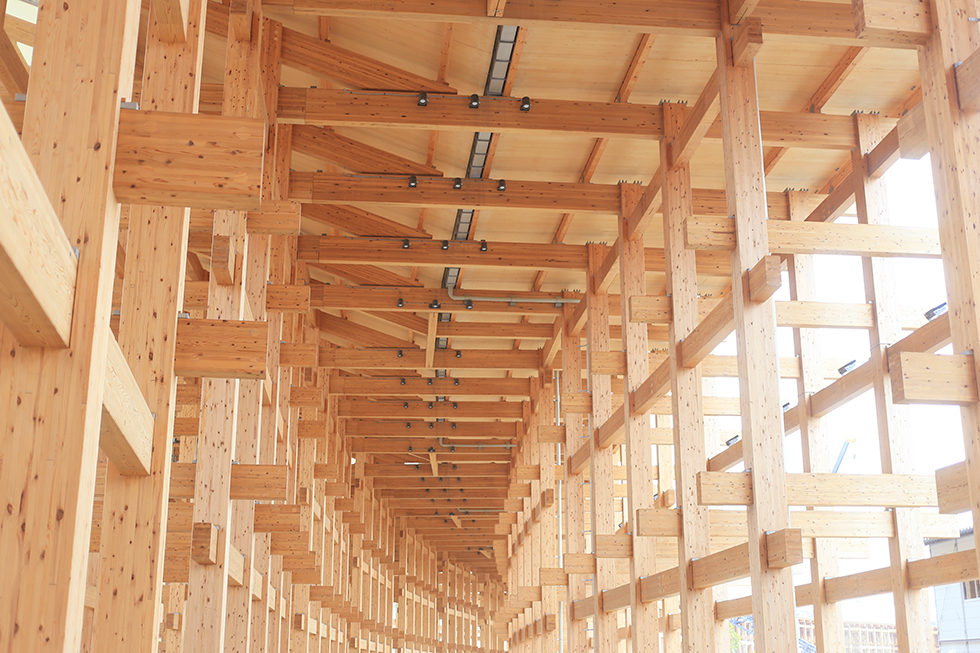